Cumminalong
Doghouse Diesel Performance
Got started on the block stiffener to accept the main studs today.
The main studs are not a drop in fit, you do have to drill the block stiffener to clear the sutds and nuts.
Careful layout is critical here, otherwise you'll mangle the stiffener.
Measure, measure, measure......
Here you can see how much clearance you need to gain.....
Measure your center to center distance on the studs and carefully lay everything out on the stiffener before cutting or drilling.....
Drill your pilot holes and verify alignment before drilling your main holes.....
Once you're happy, get to work.....
Modified Block Stiffener.....
The main studs are not a drop in fit, you do have to drill the block stiffener to clear the sutds and nuts.
Careful layout is critical here, otherwise you'll mangle the stiffener.
Measure, measure, measure......
Here you can see how much clearance you need to gain.....
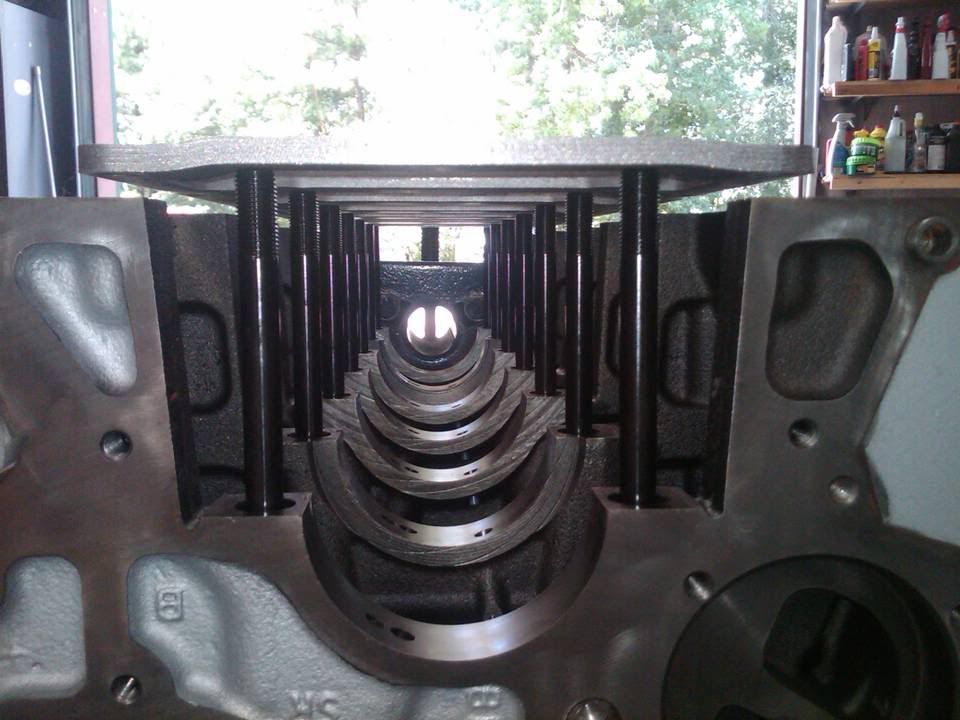
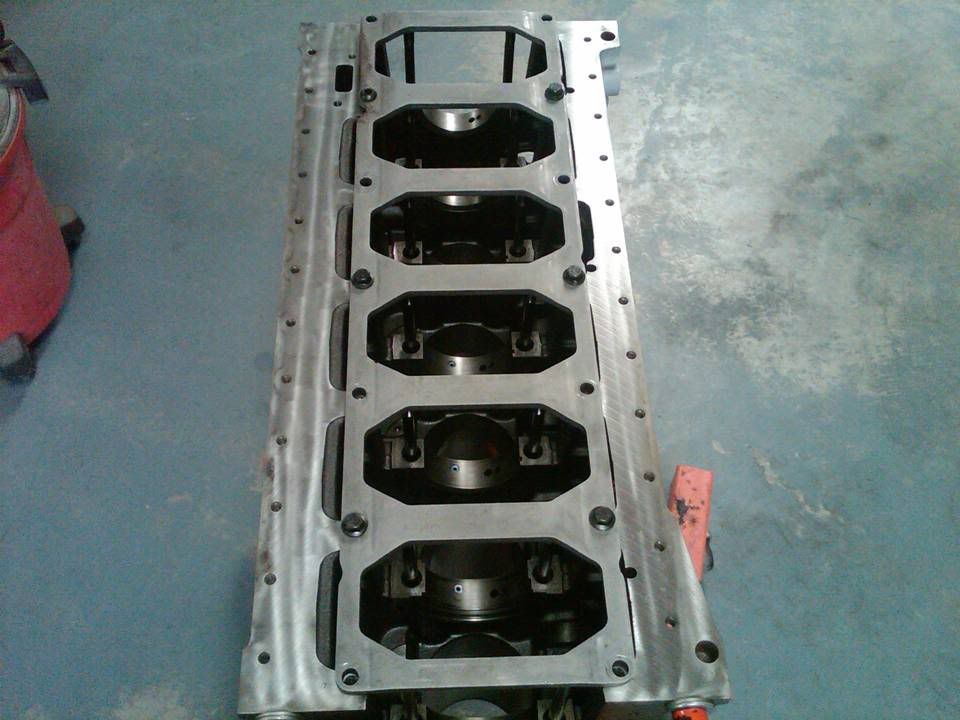
Measure your center to center distance on the studs and carefully lay everything out on the stiffener before cutting or drilling.....
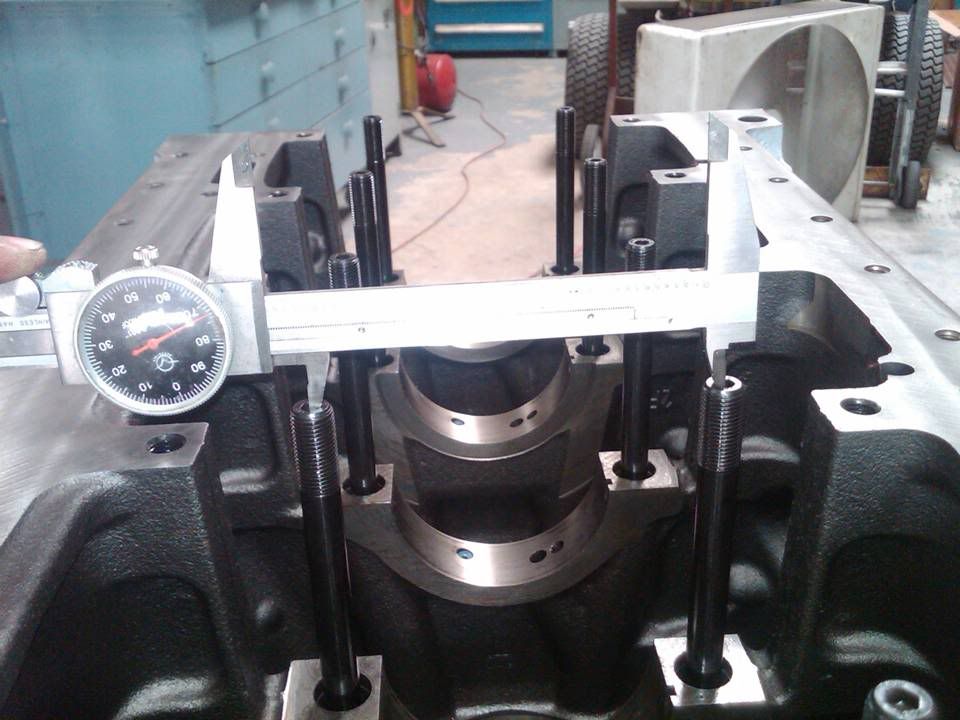
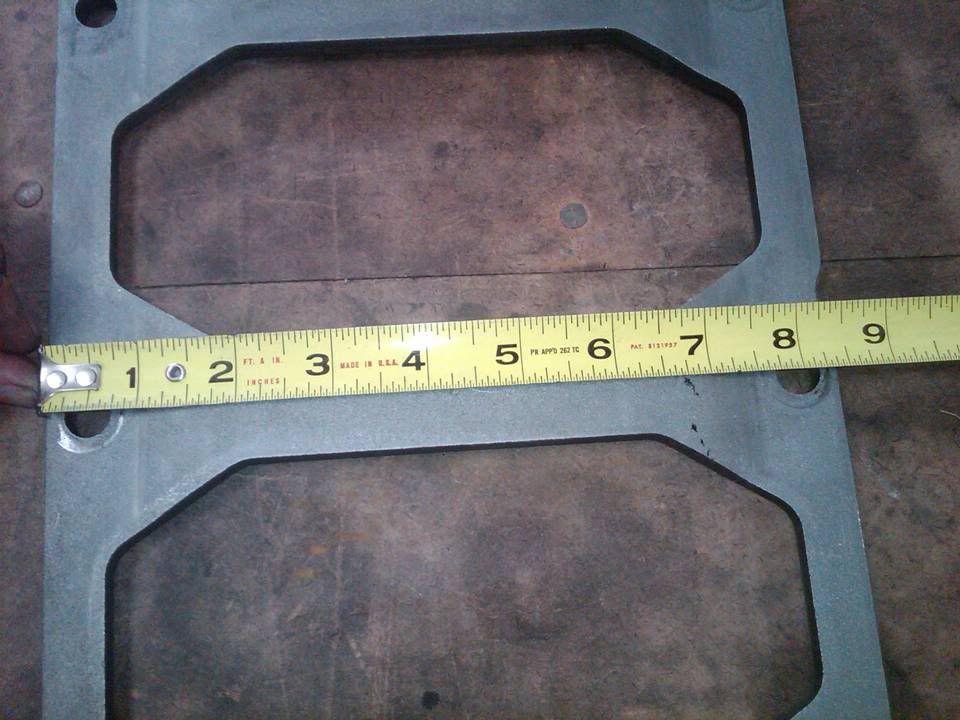
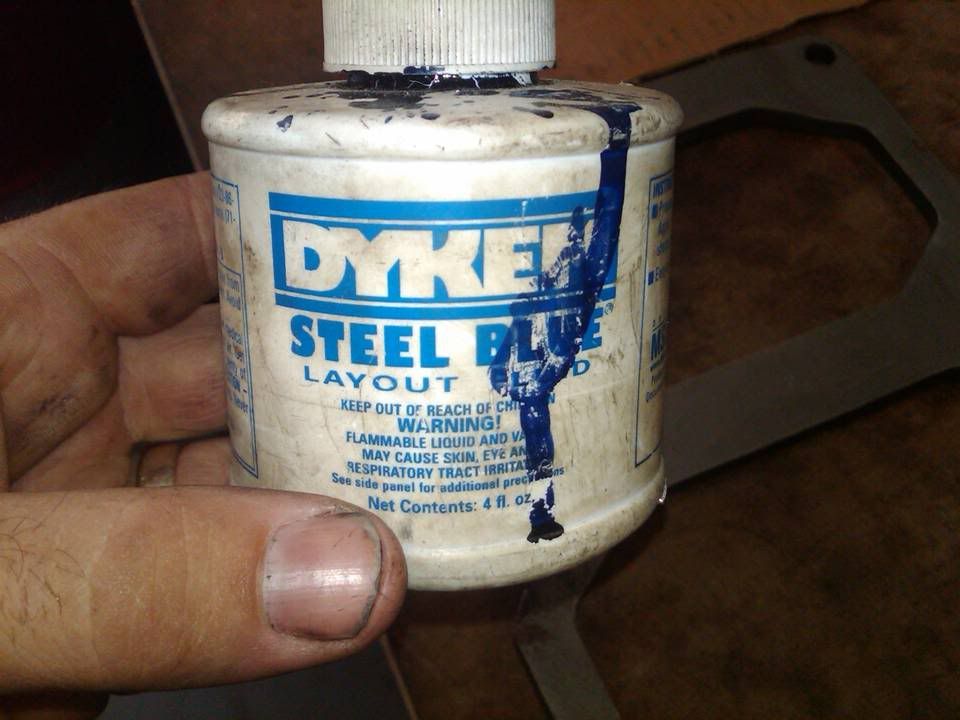
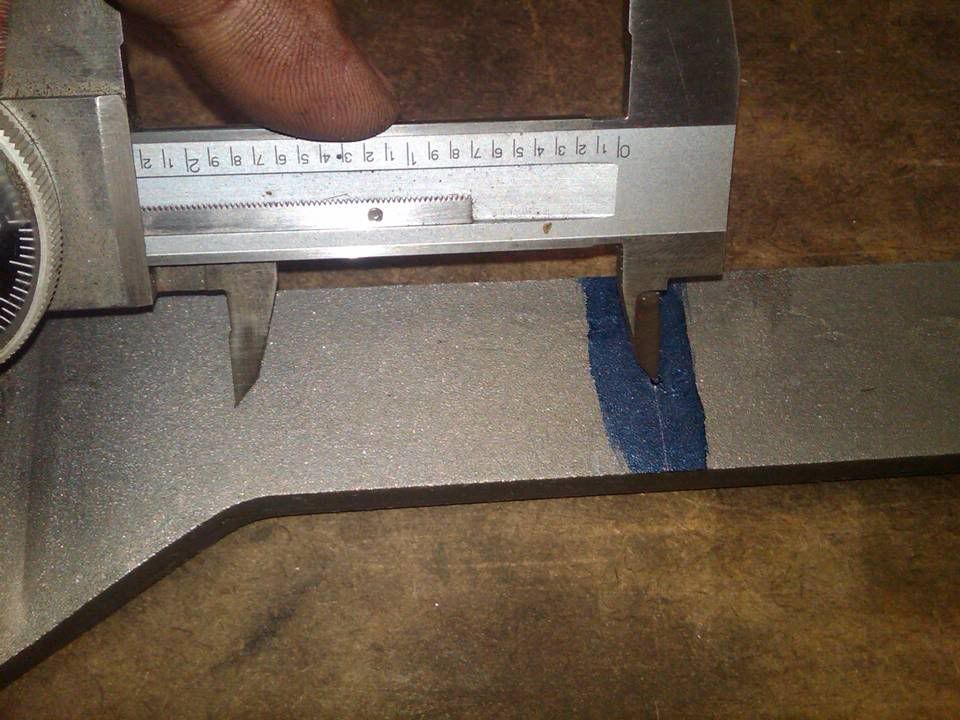
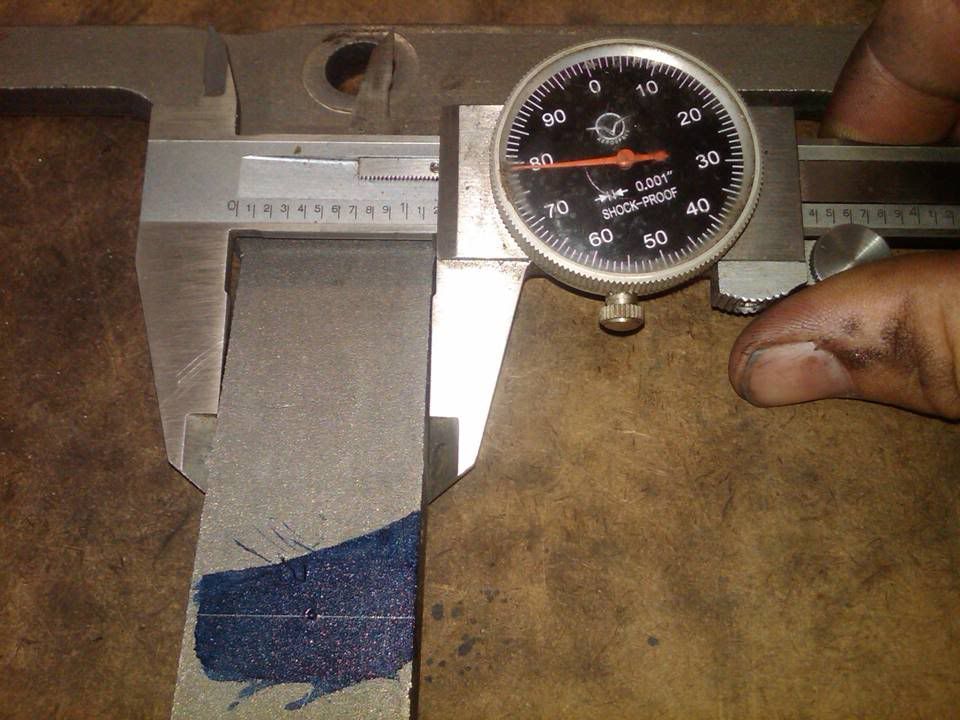
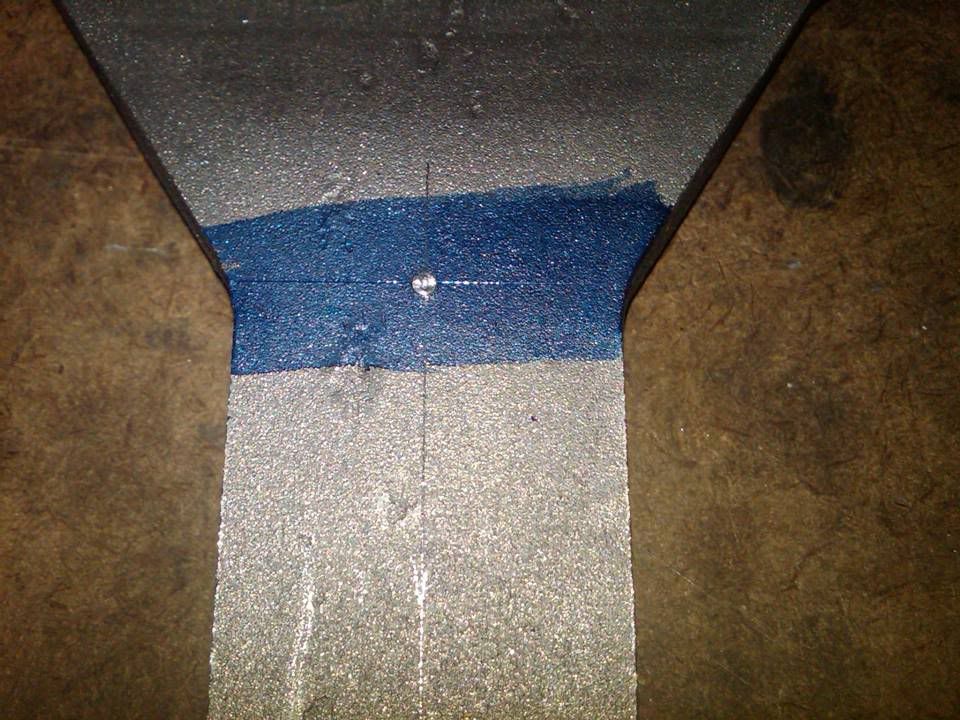
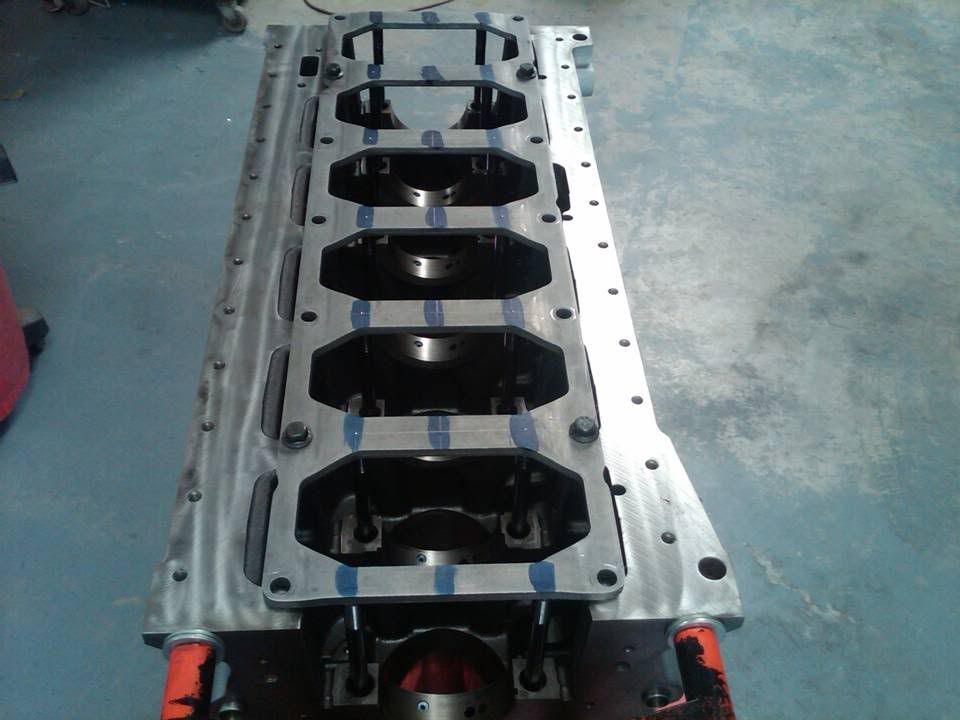
Drill your pilot holes and verify alignment before drilling your main holes.....
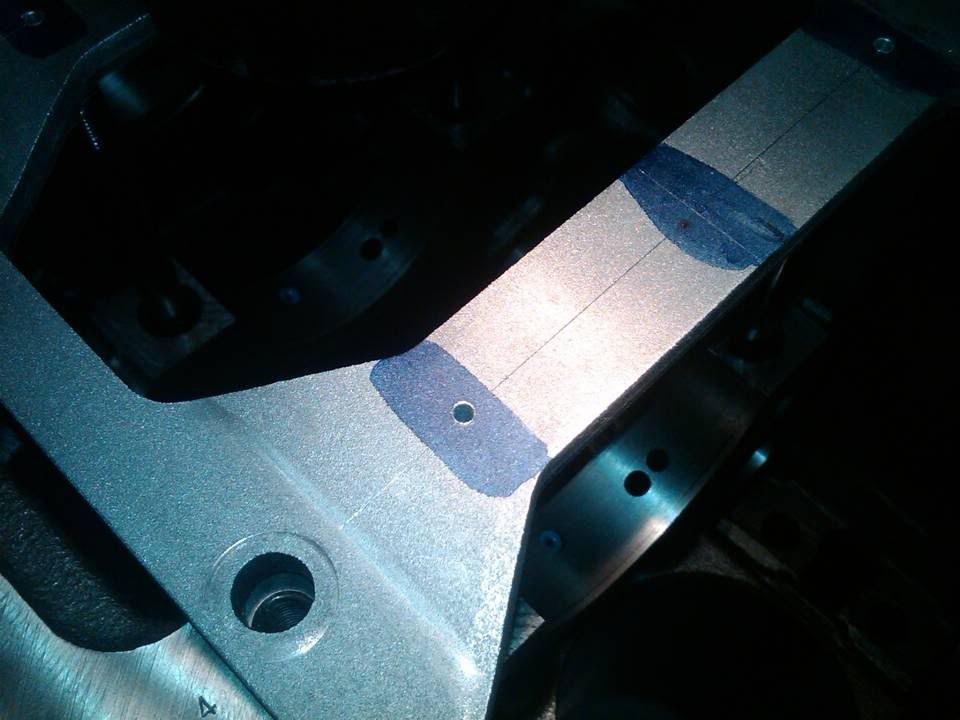
Once you're happy, get to work.....

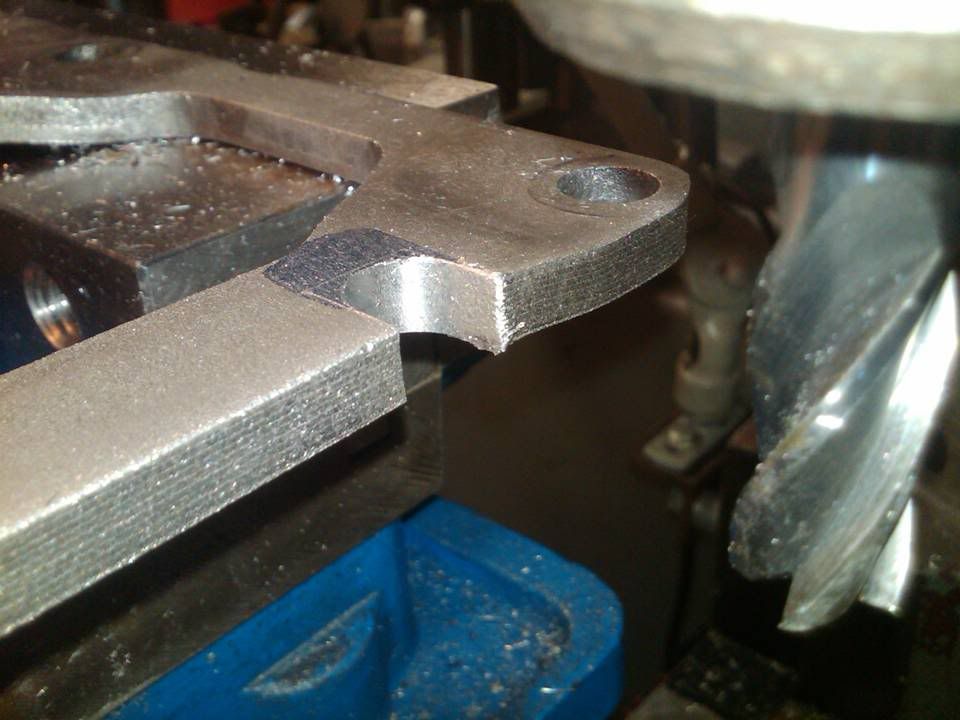
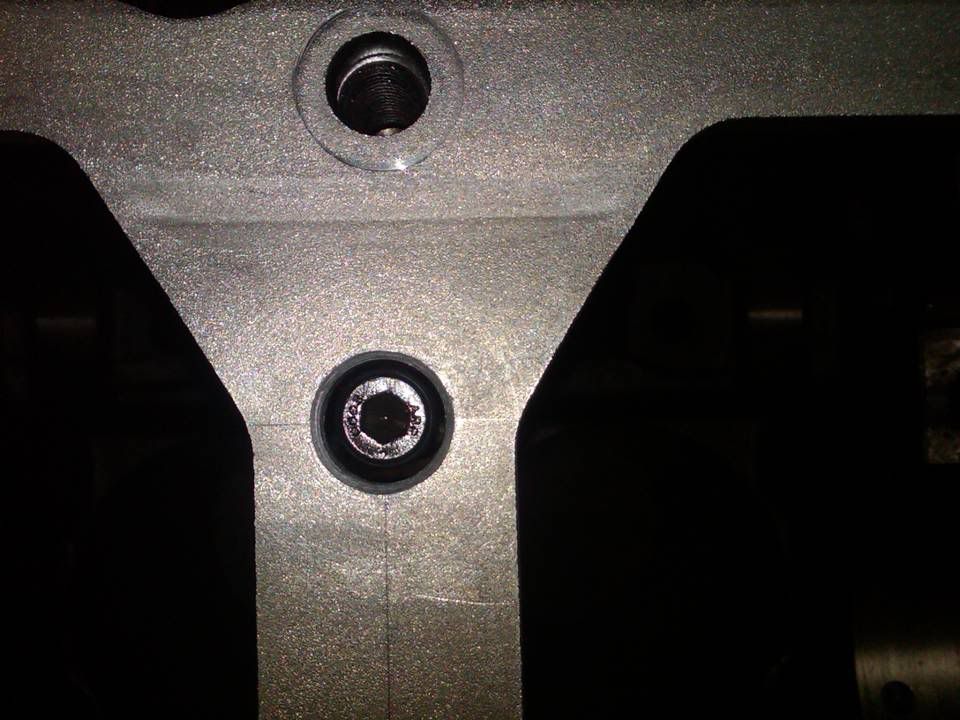
Modified Block Stiffener.....
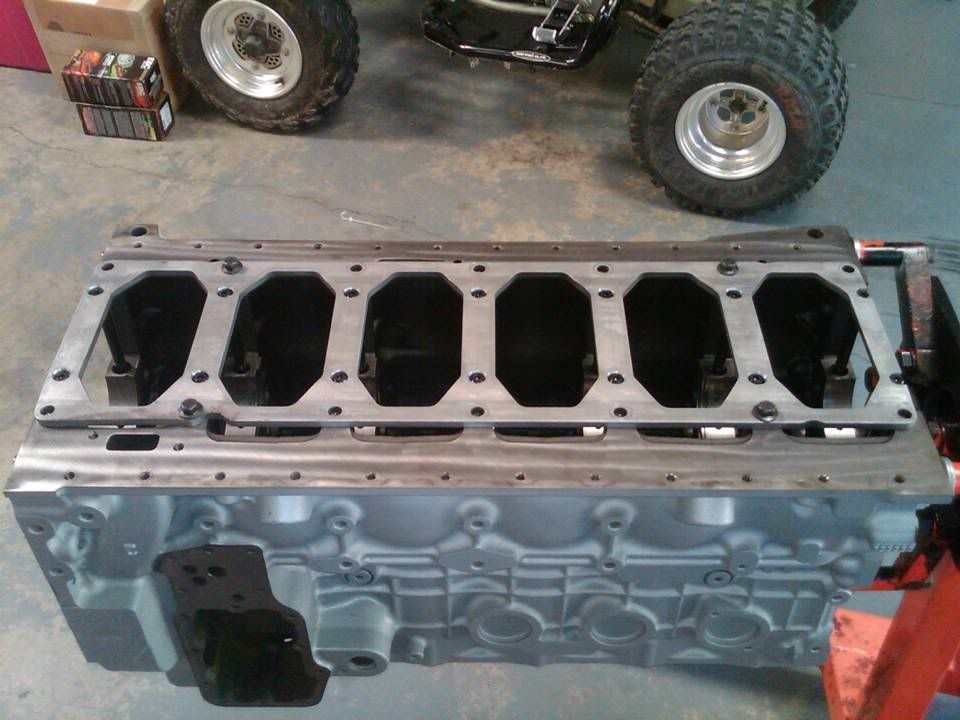