MrMarty51
Well-Known Member
Got the seal removal tool from ebay. It worked great. Had to file the shift shaft slightly to remove some burrs, in order to get the seal removal device to slide over the shaft.
I tried pressing in on the tool and rotating it with the 3/4” wrench, not enough pressure, I must have turned into a weakling in my old age. Removed the puller bolt from the end. Used the brass/mag hammer and tapped the tool while turning it with the wrench. That worked wonderfully.
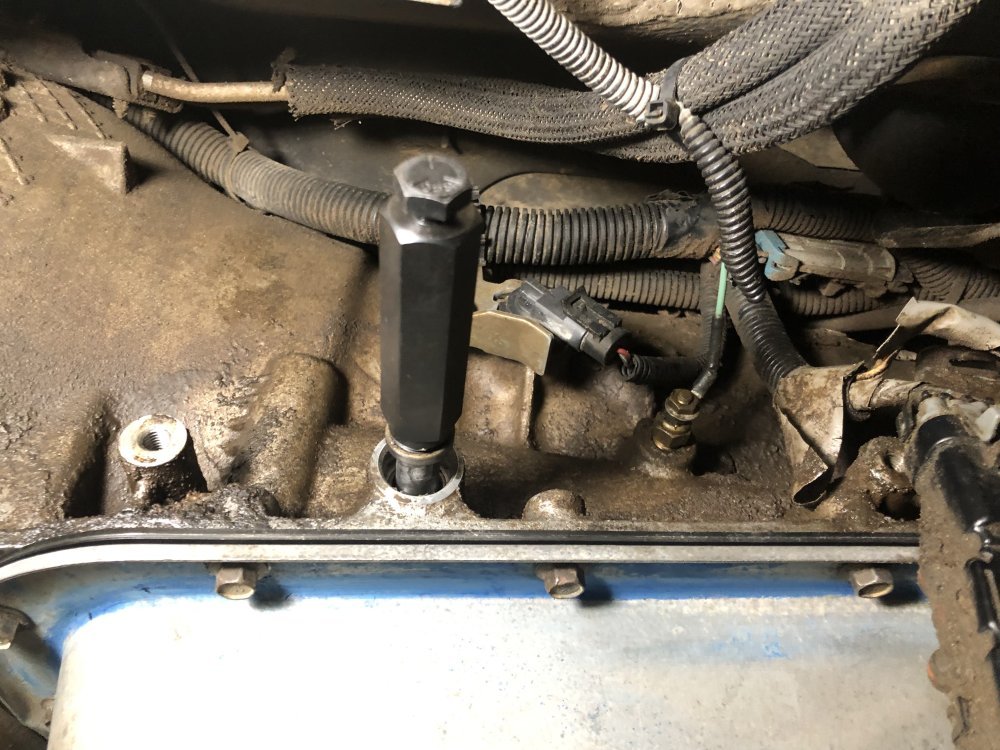
The kit came with a new seal and a seal driver sleeve. That also was a mighty fine unit to add to the tool collection.
Coated the OD of the new seal with no1 permatex, Seal lips with some lube and the little seal driver punched it right to home.
The seal that came with the tool kit looked more substantial than the CR seal I had bought so I installed the seal furnished with the kit.
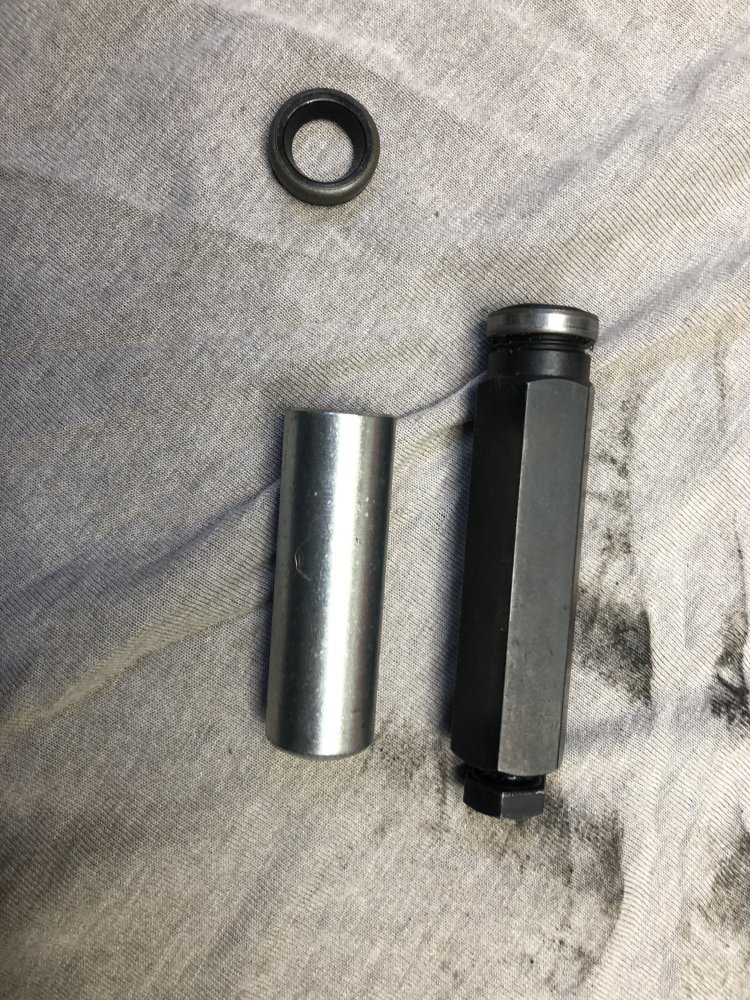
For about $20.00 this kit should be in every tool box.
I tried pressing in on the tool and rotating it with the 3/4” wrench, not enough pressure, I must have turned into a weakling in my old age. Removed the puller bolt from the end. Used the brass/mag hammer and tapped the tool while turning it with the wrench. That worked wonderfully.
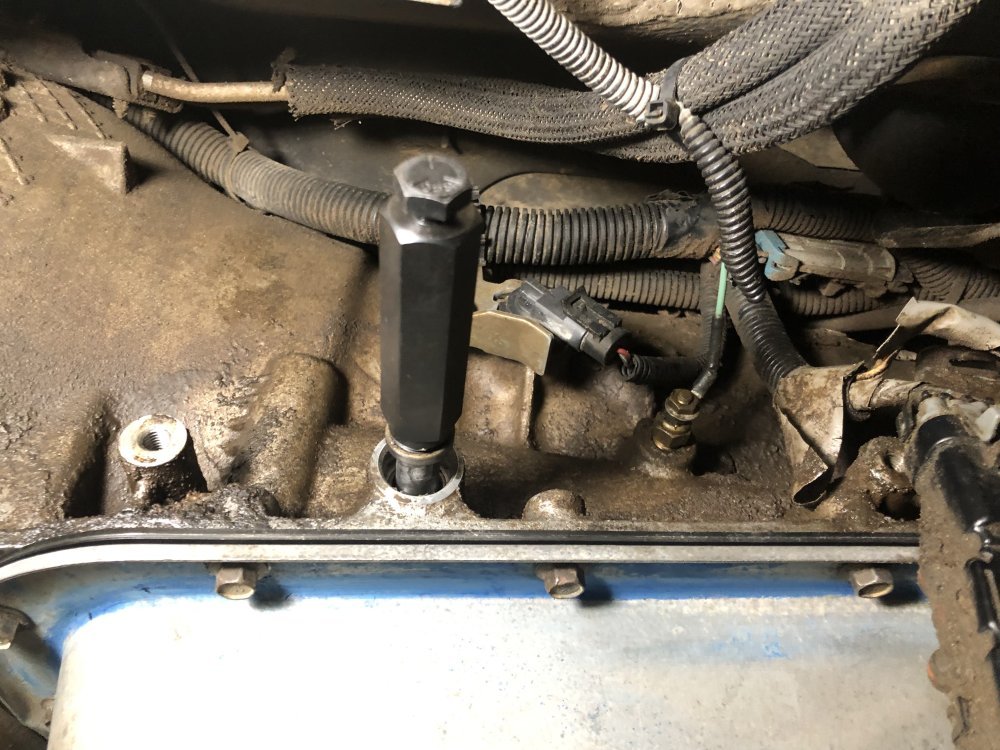
The kit came with a new seal and a seal driver sleeve. That also was a mighty fine unit to add to the tool collection.
Coated the OD of the new seal with no1 permatex, Seal lips with some lube and the little seal driver punched it right to home.
The seal that came with the tool kit looked more substantial than the CR seal I had bought so I installed the seal furnished with the kit.
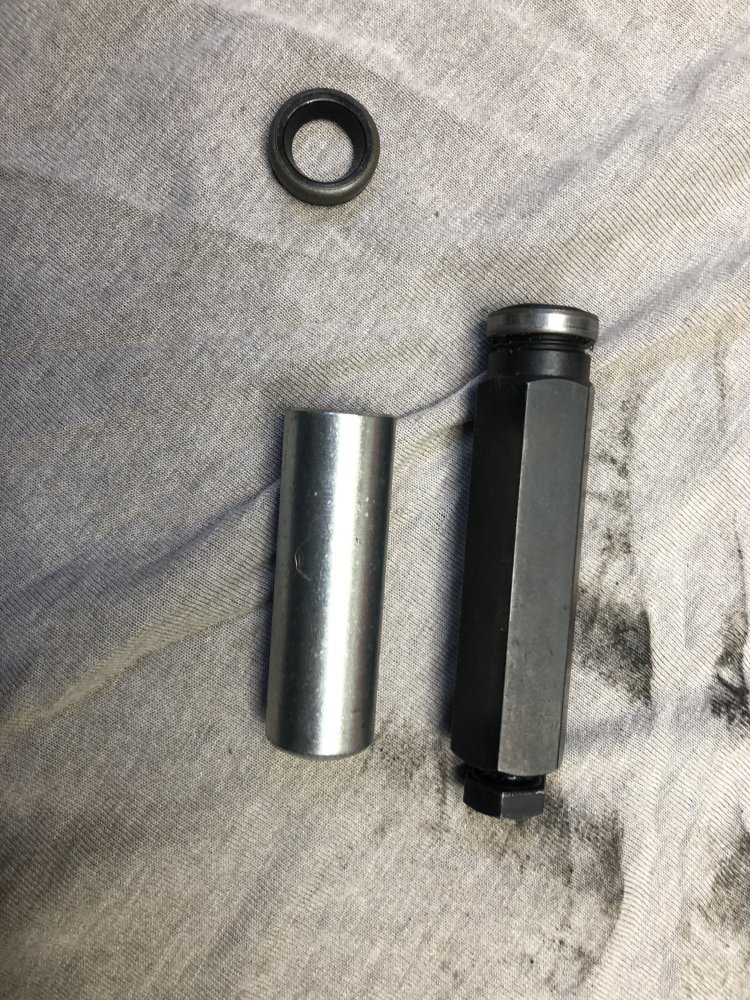
For about $20.00 this kit should be in every tool box.