Rockabillyrat
SlIgHtLy StUpId.
Well I drank entirely too much rum on Friday. So needless to say my Saturday was unproductive. But I had some time today to get back to work. Decided to switch gears since I'm waiting on the axle shims so I started working on the sway bars. The rear seemed like a good place to start. I'm using a 1" torsion style sway bar from Tk1. But I'll be making my own frame mounting brackets because the ones in the kit felt "cheap" to me. They are made from .125" with a 90* bend. I decided to step up to a .180" piece of box steel to make my mounts from. Box steel is awesome if you want a nice looking piece and don't have a press brake. I've been using it alot on this project. I liked the look of the provided mounts so I turned them into a template. I purposely used a larger piece of steel than I needed to avoid using the weld seem in any of my new frame mounts. With every thing squared up I cut the links to length and welded the tabs to the u bolt plates.
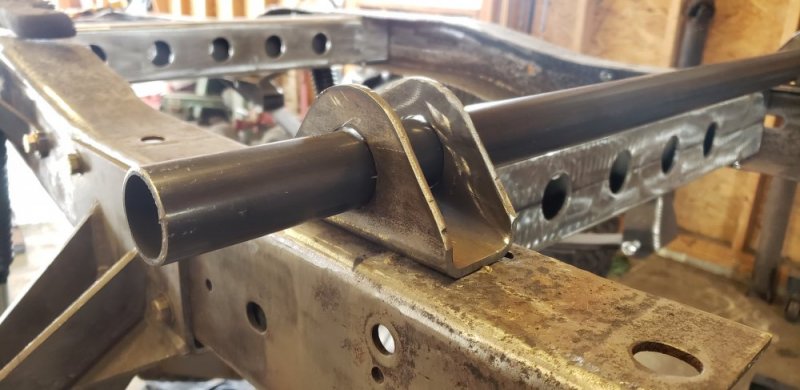
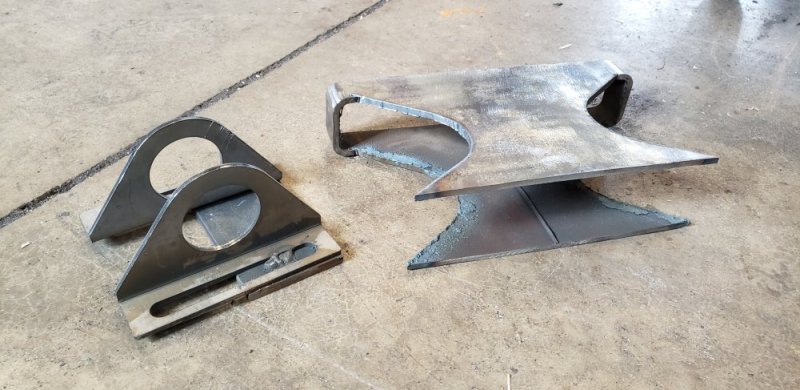
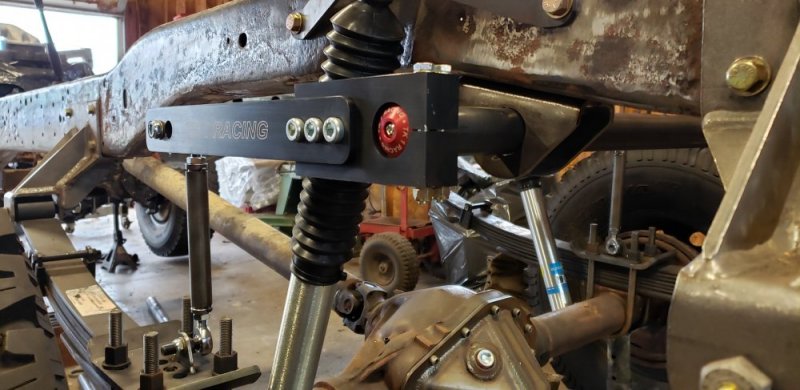
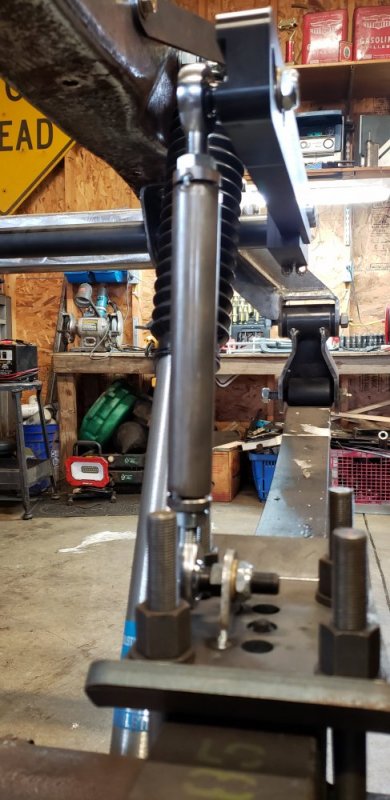
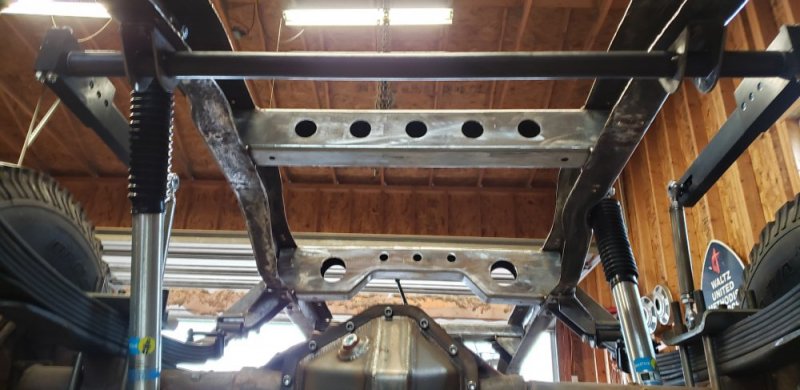
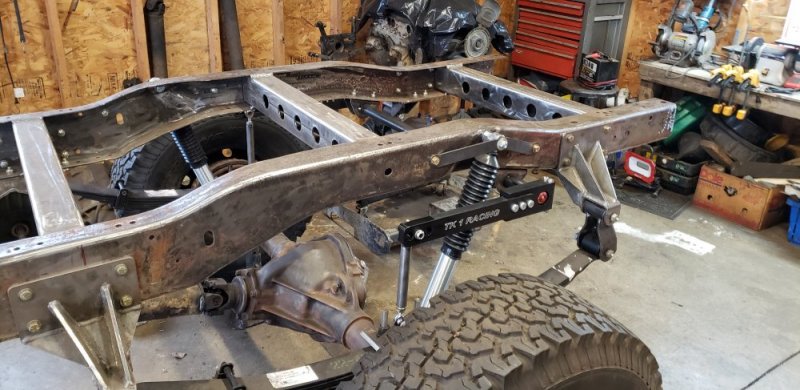
I'm going to build similar mounts for the front and get it installed next week. Then back to the crossmembers. I'm running out of time with the weather getting nice though. Thankfully I only have a few projects on the house to get done so figures crossed I wont take a 6 month hiatus from Johnny....
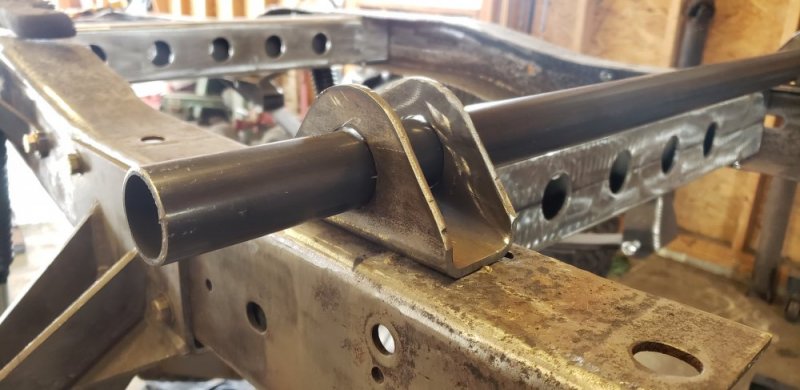
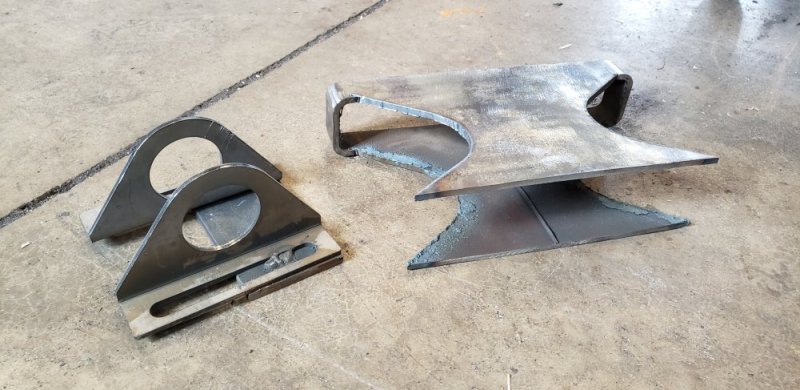
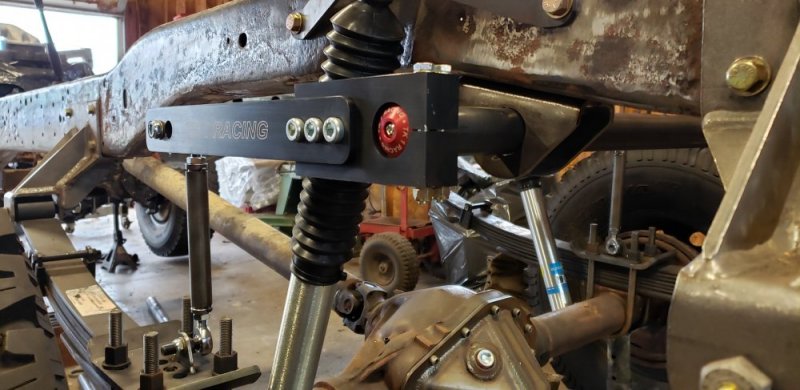
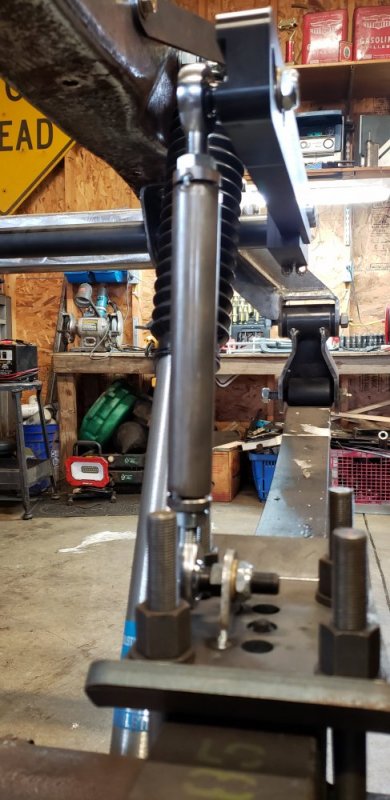
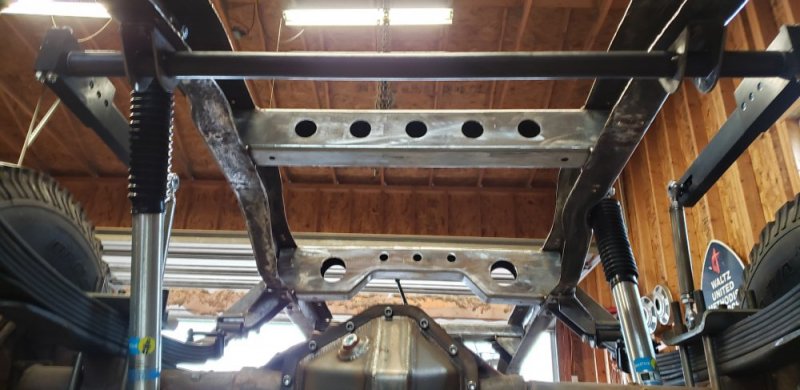
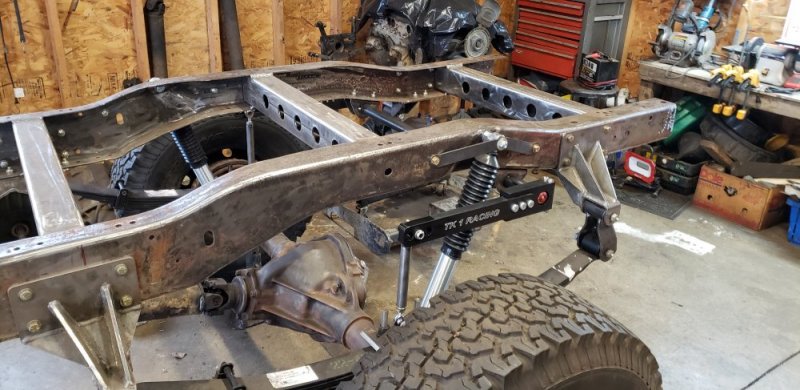
I'm going to build similar mounts for the front and get it installed next week. Then back to the crossmembers. I'm running out of time with the weather getting nice though. Thankfully I only have a few projects on the house to get done so figures crossed I wont take a 6 month hiatus from Johnny....