Paveltolz
Доверяй, но проверяй
Thanks. I didn't see this post until I had given it a test run on my -10 AN turbo return line. Proof that great minds think alike, that's just what I did tonight. I have a bottle of water mixed 10:1 with Dawn Dishsoap that I use for clean up. Worked great.Even simpler Paul is to mix dish soap and water and use a pump window cleaner bottle. Tested thousands of welds this way. Only need about two pounds of air pressure.
The only leak I saw was at the Air Pressure Stem inserted into the test plug. Ran it up to about 40 PSI it turns out. Too much but the line handles 60 psi on cold starts.
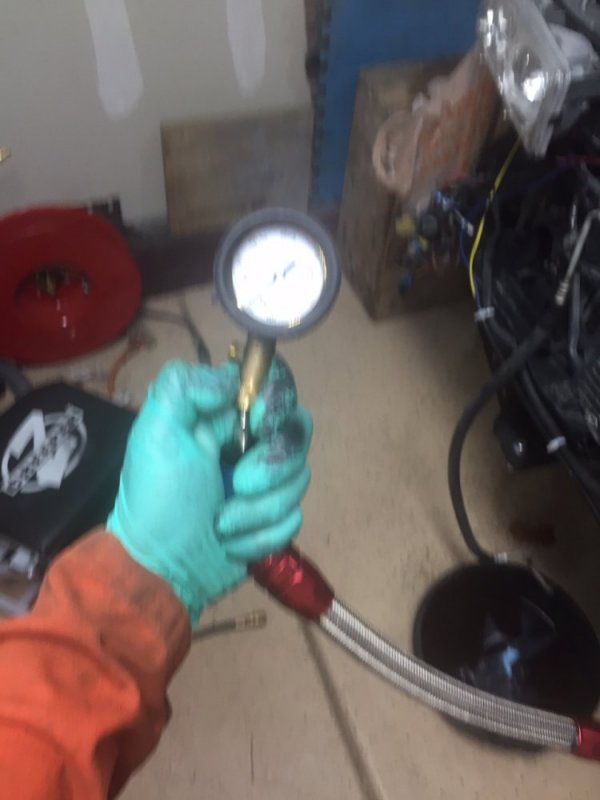
Admittedly, the picture is staged because it is too much to hold all in one hand but, it gets the point across.