All the regular manifolds I've done over the years went on clean and dry, and only if it leaked (way rare) did it get a gasket- but that is cast manifolds.
On the steel hummer headers, I only delt with maybe 15 installs. Most of them get the regular felpro gaskets I mentioned.
I forgot it has been 3 years already- yeah, kinda hard to push that.
Most headers do not need the ports connected, but with the design on yours, I can't see how they are not. Stainless steel (almost all types) expand massively, ESPECIALLY PIPE.
Iirc 316 is .04 factor, meaning your header is trying to expand 1/16" in length. Between that and the vibration, I can't see how rtv is viable. And you cant compare hot rods to rv. Hotrod is constantly getting checked, tweeked, things getting tightened,etc. Your rv should be like that spinning cooker- set it and forget it.
If you haven't snapped any locking retainers, and they obviously stayed tight, you just need a simple gasket. Copper gaskets are great and have there place, but idk about them here. The copper is ductile, yes. But once it flattens out, it will just keep getting malled by the vibration. Just my guess, I never used copper on a 6.5- paper always worked as long as bolts aren't coming loose. The paper can handle expansion and contraction. When the SS expands it will squish the copper more, but what about when it contracts, Won't it leak then?
I was able to locate gaskets that might work.
Remflex Performance Promise
• Seals Warped Flanges:
Remflex exhaust gaskets come in a standard 1/8-inch thickness and are designed to crush 50%. This allows them to fill gaps in the flange surface up to 1/16-inch!
• Won’t Burn Out:
100% flexible graphite construction means Remflex gaskets are good for up to 3,000 degrees F—far exceeding that of any vehicle’s exhaust system temperature!
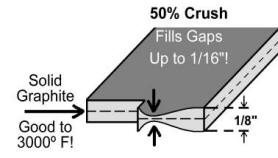
• No Re-Torquing Necessary:
Remflex exhaust gaskets rebound 30%, creating an optimum seal that eliminates the need to re-torque!
About Remflex
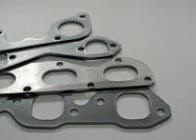