Will L.
Well-Known Member
If Peninsular doesn't have a fix, i would start with having some braces welded from flange to flange. Then checking for & surfacing like he is saying.
Hummer headers dont have the braces, but they can expand between flanges and not distort. Because the ports are not tied together by a pipe that can expand linear between them.
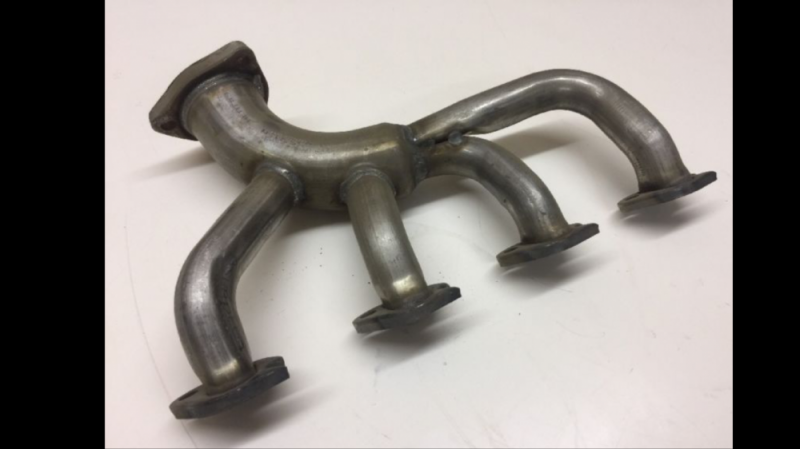
Hummer headers dont have the braces, but they can expand between flanges and not distort. Because the ports are not tied together by a pipe that can expand linear between them.
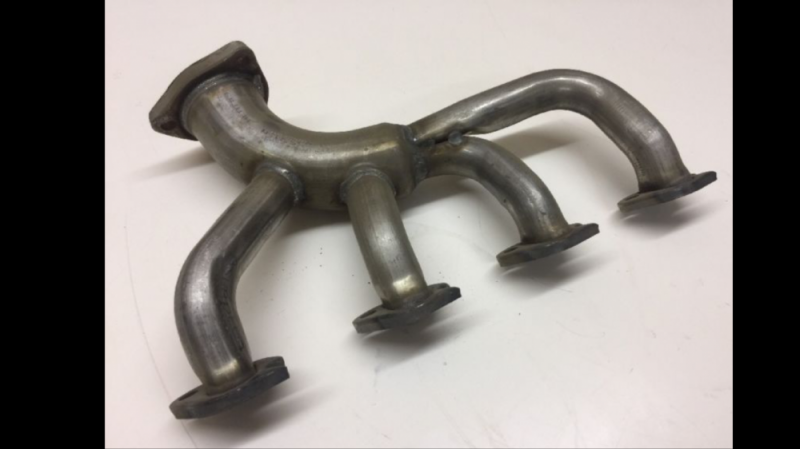