chevyCowboy
I might be crazy but i ain't dumb
A little over a week ago a buddy told me about a garage in town that was possibly free for the taking, I said that would be sweet try and find out more, that was on monday. Tuesday he saw the guy again and he said if you want it take it but I want it gone yesterday, he had plans to get his hoe there the coming weekend to push it In a pile.
Wednesday I made some calls to some buddies and started rounding up needed supplies and people to help.
The building was 24 by 38 according to city code the biggest I could do on a slab is 24 by 30 which is about all the bigger I can fit on my lot. so I had to cut 8ft off the front which was fine since I wanted to do one 18ft door instead of the 2 9ft ones that where there. Also the inside was set up with a wall down the middle and a bathroom and office on one side so that all had to be removed to get trailer in, by 10pm it was all out and cleaned up.
Friday I had to go on a little road trip to get the 20k 29ft trailer that we where going to use, also had to get plans submitted.
Got the 8ft cut off and the front reframed and the lifting beams in and walls braced by 11
We had to help one of the guys pour some concrete sat morning but where ready to start lifting by 1. Everything went smooth and had it on the trailer and moved off the slab by 430.
Just waiting on my building permit to come back before I remove my old mini shop and start to prep for the pad
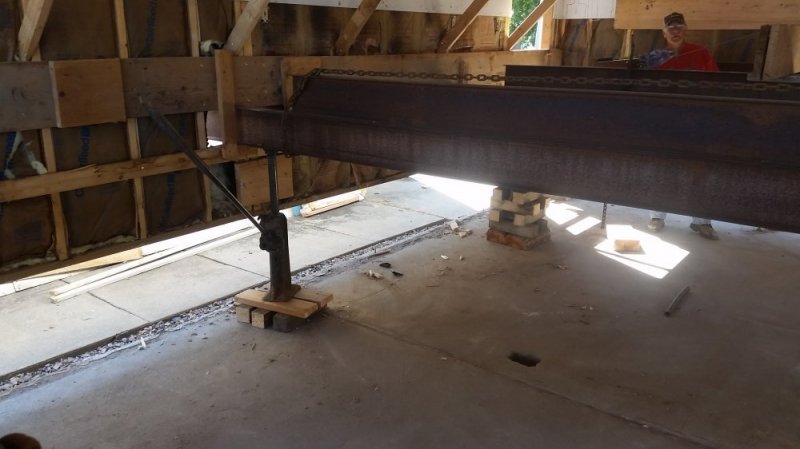
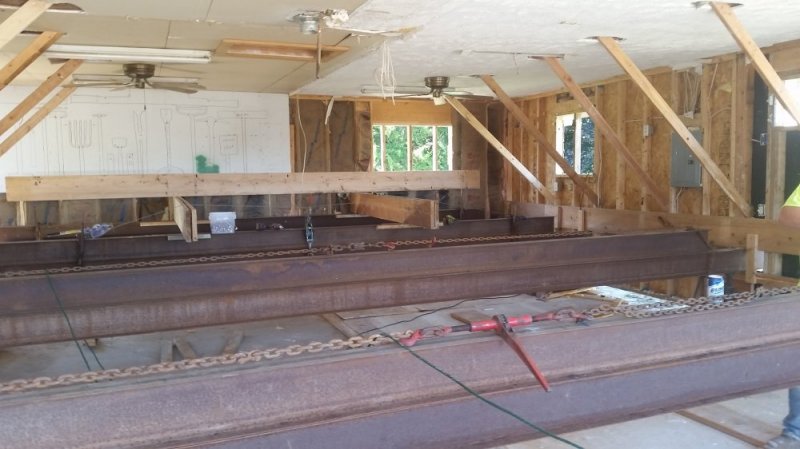
Wednesday I made some calls to some buddies and started rounding up needed supplies and people to help.
The building was 24 by 38 according to city code the biggest I could do on a slab is 24 by 30 which is about all the bigger I can fit on my lot. so I had to cut 8ft off the front which was fine since I wanted to do one 18ft door instead of the 2 9ft ones that where there. Also the inside was set up with a wall down the middle and a bathroom and office on one side so that all had to be removed to get trailer in, by 10pm it was all out and cleaned up.
Friday I had to go on a little road trip to get the 20k 29ft trailer that we where going to use, also had to get plans submitted.
Got the 8ft cut off and the front reframed and the lifting beams in and walls braced by 11
We had to help one of the guys pour some concrete sat morning but where ready to start lifting by 1. Everything went smooth and had it on the trailer and moved off the slab by 430.
Just waiting on my building permit to come back before I remove my old mini shop and start to prep for the pad
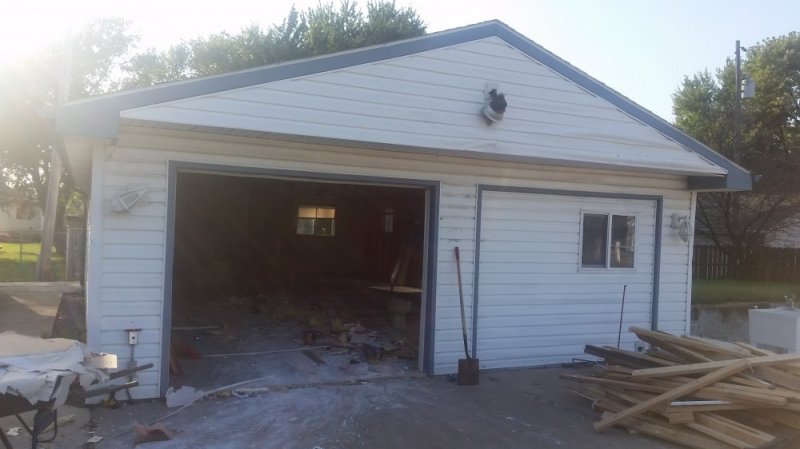
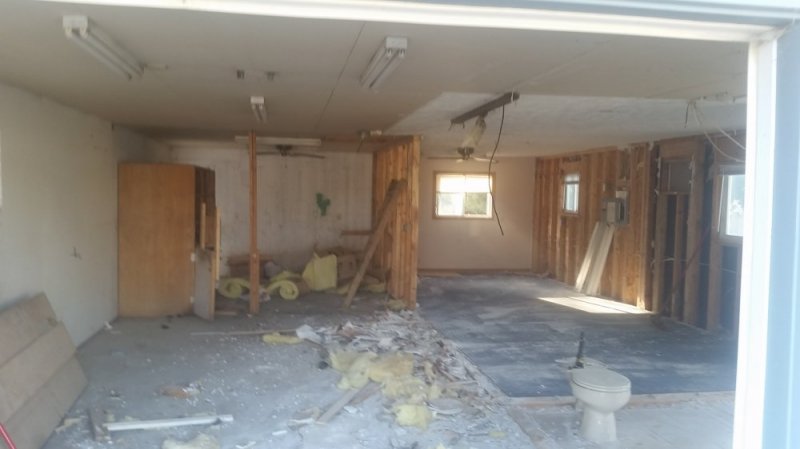
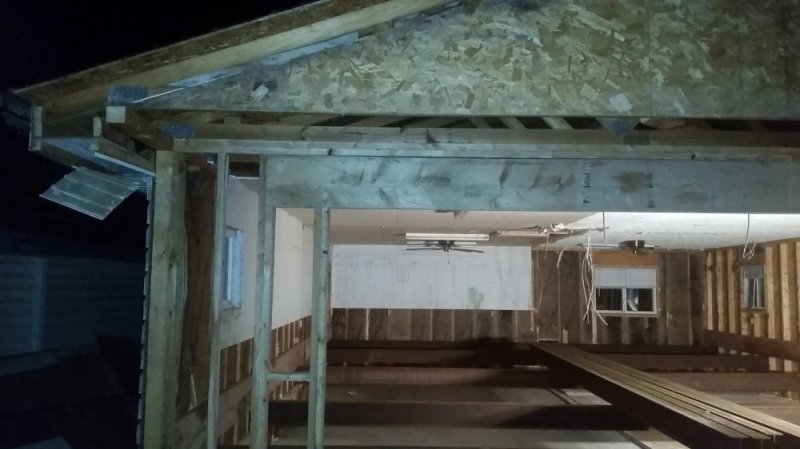
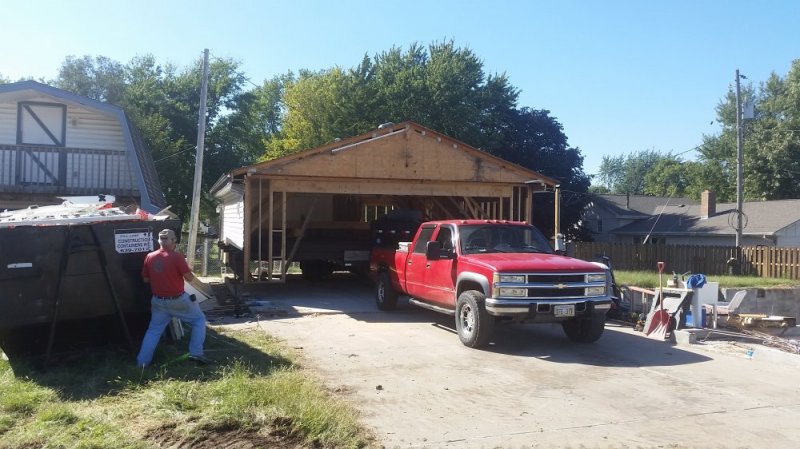
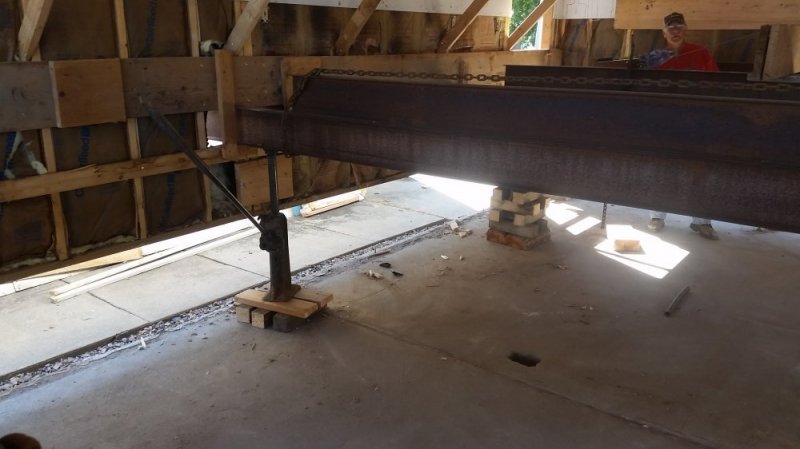
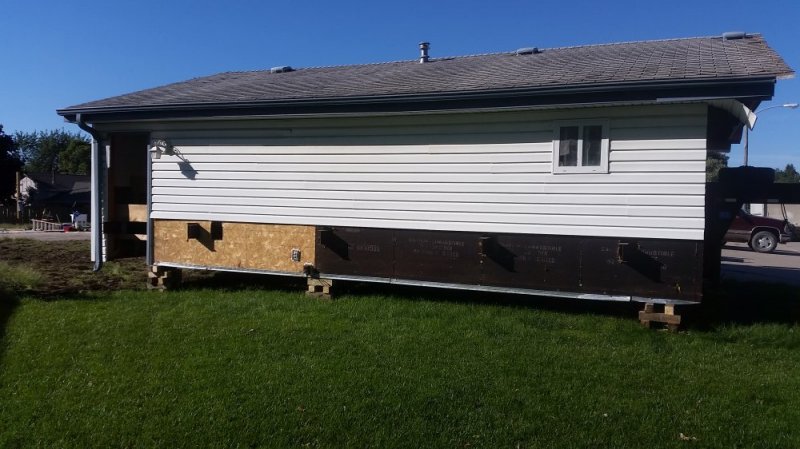
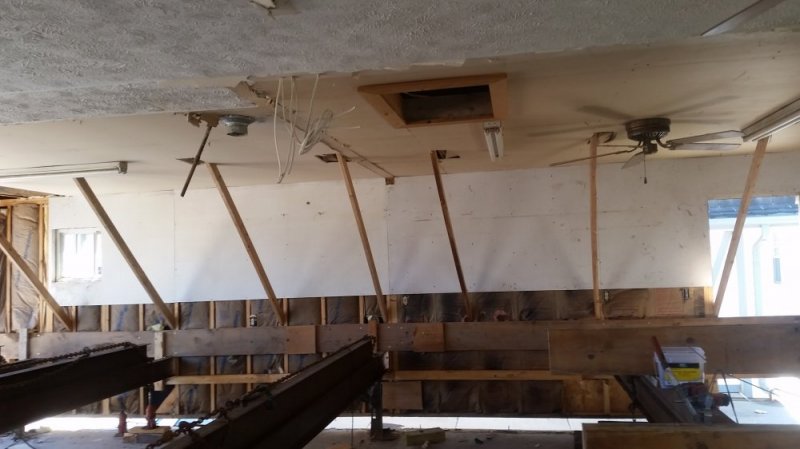
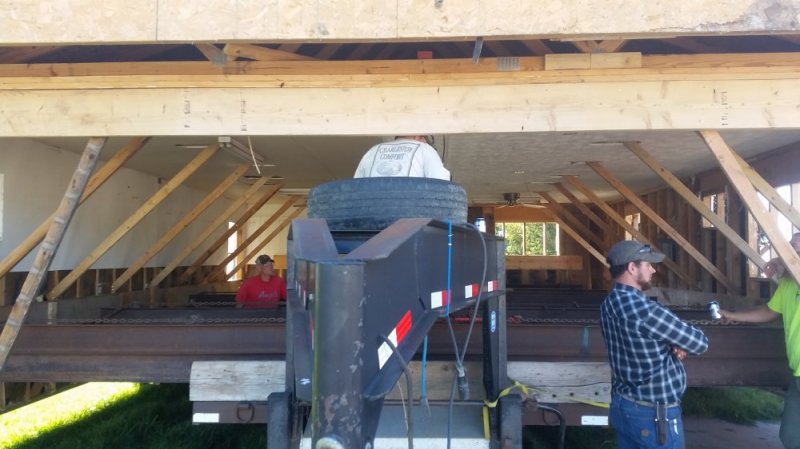
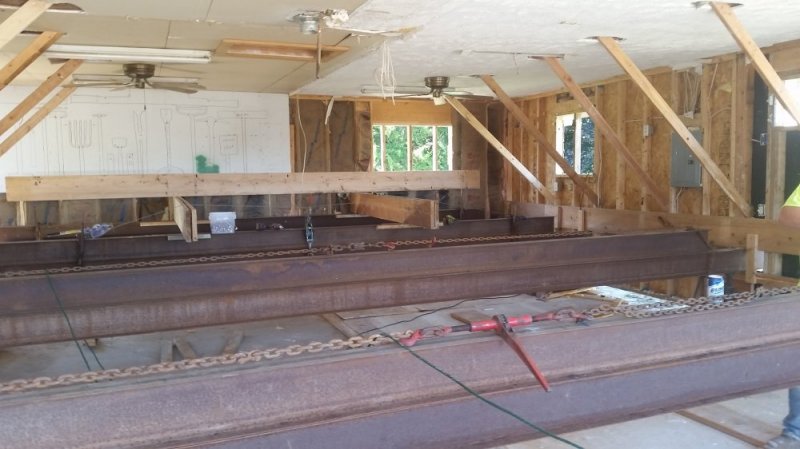