- Staff
- #41
You can compare this R12/R134 temp chart to the R134/ES chart and see that R12 and ES are much closer to each other at each interval, hence why I recommend using the R12 switch vs the R134 retrofit switch.Regular with dye. Use R134a pressure switch.
Enviro-Safe R134a Replacement Refrigerant W/ Dye 6 oz Cans & Cases #1030 | Enviro-Safe Refrigerants, Inc.
For automotive and other R134a applications. Equivalent to 16 oz of R134www.es-refrigerants.com
Regular ES on left and the industrial on the right. Note the pressure around 32F where industrial is way higher. It's ~20F when the R134a pressure switch opens. Charts are half-assed only going up to 133 degrees... Need to go up to 200F and 500 PSI where systems explode from pressure. Note the lower head pressures on the high side at 133F.
View attachment 66018
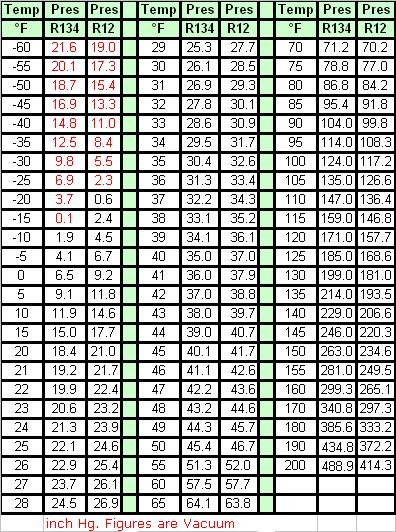