dbrannon79
I'm getting there!
Well I have been wanting to adapt something up on the tester to check the gauge accuracy. This evening while I was at work, I found a hydraulic compression tee that had 1/4" tube on the ends and a 1/8" npt thread with an adapter for 1/4" npt, made up a test line using an old injector line to check how accurate the tester was. Got home and cobbled this contraption together.
I was very cautious applying pressure to it once I got it all together since I don't like compression fittings with this much pressure. slowly applied pressure watching for leaks and standing as far back as my arms would allow!!
watched as both gauges rose noticing right away that the one I added was showing right at 100 psi higher than the tester. this stayed steady all the way up to 2000 psi, both were 100psi apart from each other.
then I attempted to make the injector pop and almost maxed out the little 3000 psi gauge each time while the one on the tester was showing close to 2000psi as the injector chattered spraying fuel.
If I am seeing this correctly, I think the flow is slow to move the tester gauge and the real pressure is shown on my contraption. should I go back removing all shims where before they were chattering at 1200 on the tester and see what this adaptation I made is showing?
What's everyone's thoughts here?
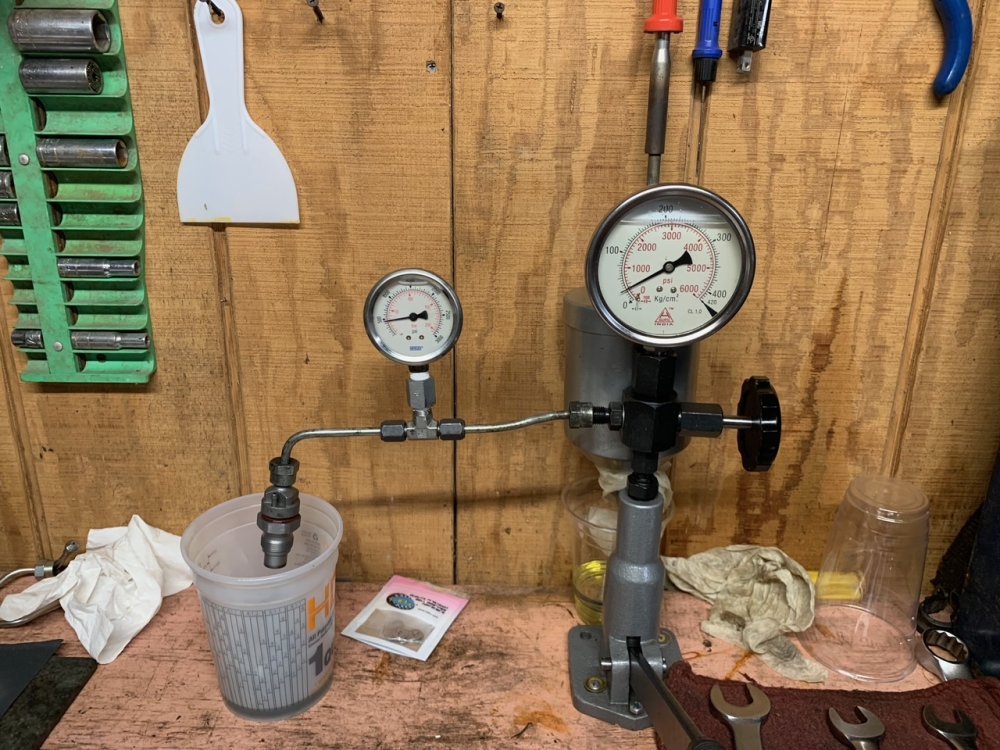
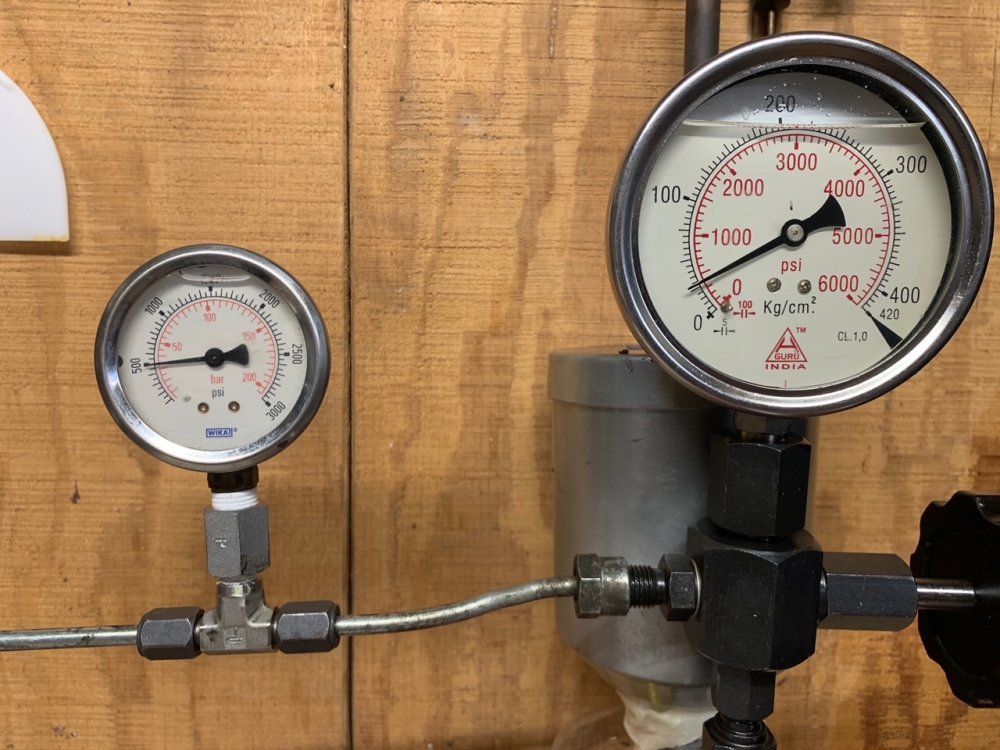
I was very cautious applying pressure to it once I got it all together since I don't like compression fittings with this much pressure. slowly applied pressure watching for leaks and standing as far back as my arms would allow!!
watched as both gauges rose noticing right away that the one I added was showing right at 100 psi higher than the tester. this stayed steady all the way up to 2000 psi, both were 100psi apart from each other.
then I attempted to make the injector pop and almost maxed out the little 3000 psi gauge each time while the one on the tester was showing close to 2000psi as the injector chattered spraying fuel.
If I am seeing this correctly, I think the flow is slow to move the tester gauge and the real pressure is shown on my contraption. should I go back removing all shims where before they were chattering at 1200 on the tester and see what this adaptation I made is showing?
What's everyone's thoughts here?
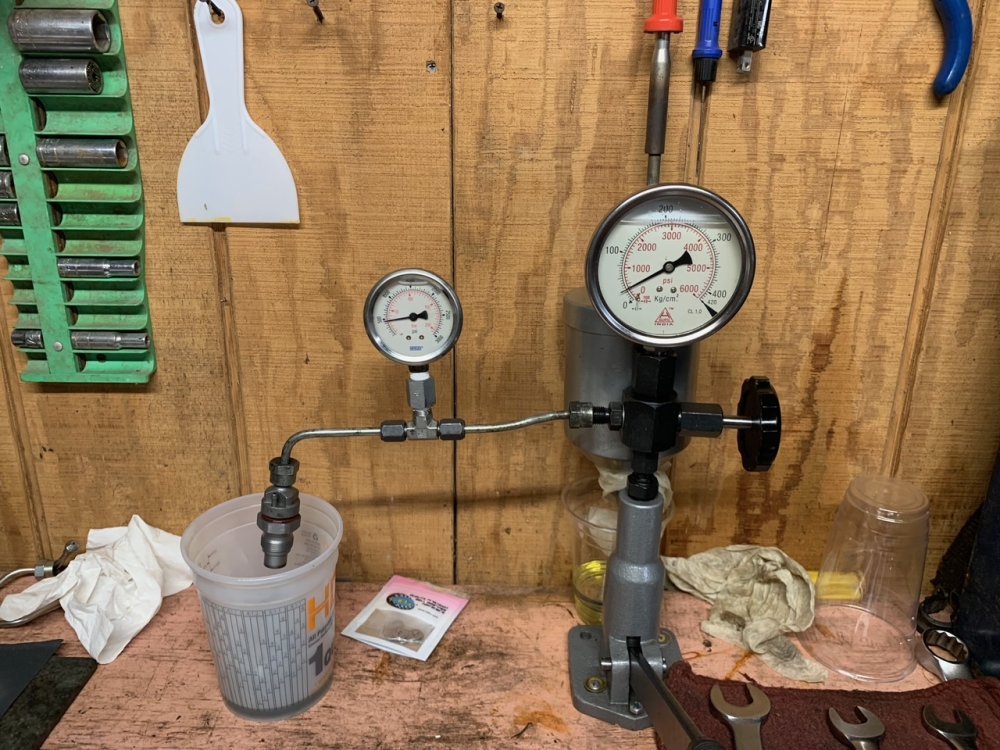
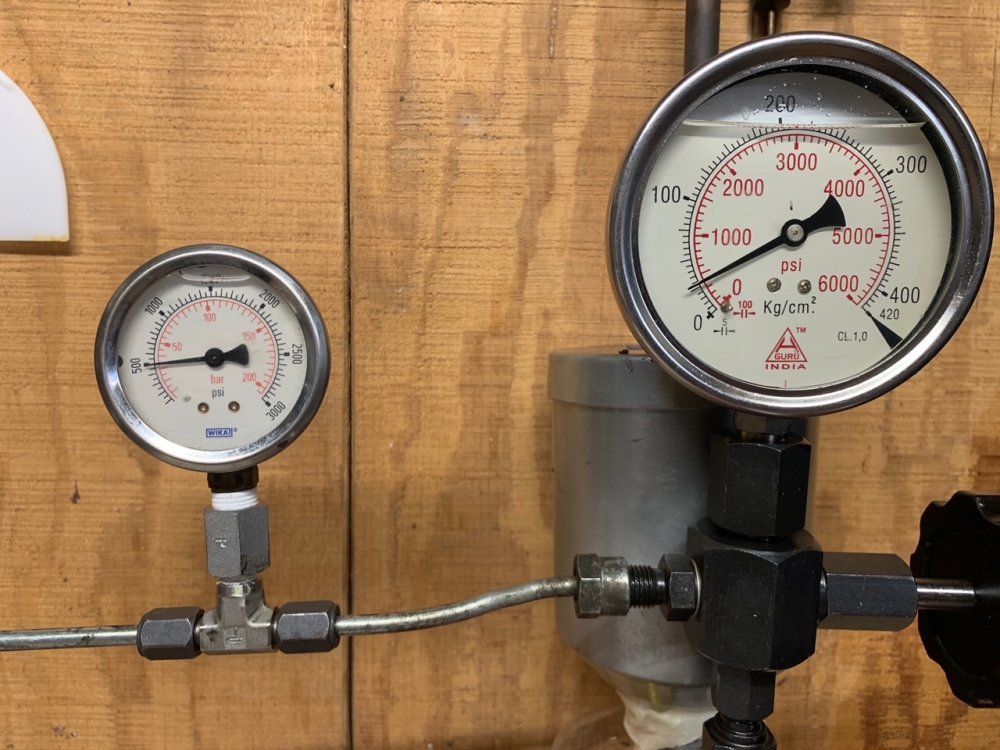