I have always like "simple" This new Fuel pressure tap will make it very easy to add a fuel pressure gauge to your truck. Alot of pepole hold off on putting a gauge in the 6.5 trucks because there is not a real easy way, until now.
This a new product I am making and have in stock ready to ship $30.
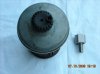
Just remove the original plastic air bleed on the fuel filter.
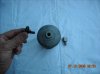
Install the new fuel pressure tap. It has an oring that will seal on the filter.
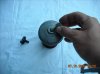
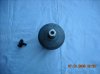
It has 1/8" pipe so you can install a electric sending unit.
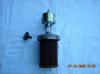
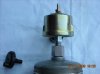
You can also use a mechanical gauge set up.
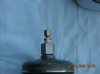
This a new product I am making and have in stock ready to ship $30.
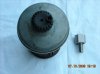
Just remove the original plastic air bleed on the fuel filter.
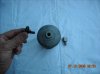
Install the new fuel pressure tap. It has an oring that will seal on the filter.
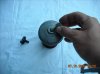
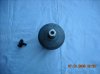
It has 1/8" pipe so you can install a electric sending unit.
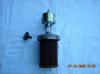
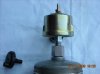
You can also use a mechanical gauge set up.
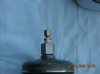