great white
Well-Known Member
Just posting for my own future reference.
The Indirect Injection Engine (IDI)
A later development was the IDI engine that utilises a separate combustion chamber, connected to the engine cylinder, into which the fuel is injected and combustion is initiated.
A heat resistant insert with low heat conductivity is located within the combustion chamber so it quickly heats up and retains heat from combustion, providing extra heat to enable quicker ignition. The fuel is injected into the hot combustion chamber as a jet at a low pressure compared to the fine high-pressure spray of a DI engine. The fuel jet hits the hot insert where ignition is initiated; the fuel is distributed around the combustion chamber as combustion continues. The expanding burning fuel, along with partially burnt and unburnt fuel, is carried into the hot engine cylinder where further oxygen is available and combustion continues.
The most common prechamber format utilised is the Ricardo Comet design developed by Ricardo and Company of Shoreham, Sussex, UK. With this design air is pushed from the cylinder into a circular ‘swirl chamber’ through a tangentially aligned throat. The bottom half of the chamber along with the throat is constructed from a nimonic alloy designed to maintain high temperatures during engine operation. The temperature of the compressed air is raised further while passing through the throat. A vigorous swirl motion is initiated as the air is forced into the circular swirl chamber. The fuel is injected into the swirl chamber and rapidly atomised within the mass of hot turbulent air.
Photo:Bosch
IDI engine – Picture shows fuel being injected into a swirl chamber with a heated glow plug – not shown is the throat from the engine cylinder to the swirl chamber - Note the lower half of the chamber constructed from nimonic alloy.
Mercedes IDI engines utilised a different design in which a jet of fuel is fired at a ball like baffle surface. The jet is broken by the baffle surface and distributed around the prechamber being finely dispersed by the turbulent air charge. Upon combustion the fuel/air mixture is carried through several bores into the main engine cylinder. Mercedes later improved this design, reshaping the prechamber, creating a swirling air motion to improve combustion.
The advantage of IDI engines is that they can operate at higher engine speeds as the more efficient fuel and air mixing provides faster combustion. Cars and small commercial vehicles require a small, light engine which must be able to operate at higher speeds to provide the necessary power, with the advent of the IDI engine the use of diesel engines in such vehicles became widespread.
The heat lost due to the increased surface areas of the combustion chamber and the pressure drop between cylinder and combustion chamber make it necessary for the engines to operate at higher compression ratios to provide enough heat for ignition. The lost heat and force required to push the air into the combustion chamber is wasted energy making IDI engines around 10-15% less efficient than DI units.
IDI engines became the engine of choice in small vehicle applications as a small engine could produce more power at higher speed providing a suitable power/weight ratio for such applications. Recent advances in fuel injection technology, which provide more precise fuel delivery, allow faster combustion within a DI engine. The improved efficiency of the DI cycle has spurred the fitment of such engines to become more common in small vehicles.
The Indirect Injection Engine (IDI)
A later development was the IDI engine that utilises a separate combustion chamber, connected to the engine cylinder, into which the fuel is injected and combustion is initiated.
A heat resistant insert with low heat conductivity is located within the combustion chamber so it quickly heats up and retains heat from combustion, providing extra heat to enable quicker ignition. The fuel is injected into the hot combustion chamber as a jet at a low pressure compared to the fine high-pressure spray of a DI engine. The fuel jet hits the hot insert where ignition is initiated; the fuel is distributed around the combustion chamber as combustion continues. The expanding burning fuel, along with partially burnt and unburnt fuel, is carried into the hot engine cylinder where further oxygen is available and combustion continues.
The most common prechamber format utilised is the Ricardo Comet design developed by Ricardo and Company of Shoreham, Sussex, UK. With this design air is pushed from the cylinder into a circular ‘swirl chamber’ through a tangentially aligned throat. The bottom half of the chamber along with the throat is constructed from a nimonic alloy designed to maintain high temperatures during engine operation. The temperature of the compressed air is raised further while passing through the throat. A vigorous swirl motion is initiated as the air is forced into the circular swirl chamber. The fuel is injected into the swirl chamber and rapidly atomised within the mass of hot turbulent air.
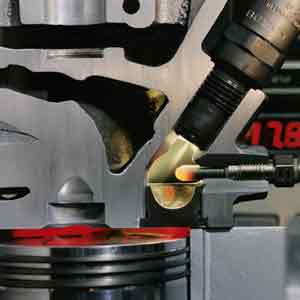
Photo:Bosch
IDI engine – Picture shows fuel being injected into a swirl chamber with a heated glow plug – not shown is the throat from the engine cylinder to the swirl chamber - Note the lower half of the chamber constructed from nimonic alloy.
Mercedes IDI engines utilised a different design in which a jet of fuel is fired at a ball like baffle surface. The jet is broken by the baffle surface and distributed around the prechamber being finely dispersed by the turbulent air charge. Upon combustion the fuel/air mixture is carried through several bores into the main engine cylinder. Mercedes later improved this design, reshaping the prechamber, creating a swirling air motion to improve combustion.
The advantage of IDI engines is that they can operate at higher engine speeds as the more efficient fuel and air mixing provides faster combustion. Cars and small commercial vehicles require a small, light engine which must be able to operate at higher speeds to provide the necessary power, with the advent of the IDI engine the use of diesel engines in such vehicles became widespread.
The heat lost due to the increased surface areas of the combustion chamber and the pressure drop between cylinder and combustion chamber make it necessary for the engines to operate at higher compression ratios to provide enough heat for ignition. The lost heat and force required to push the air into the combustion chamber is wasted energy making IDI engines around 10-15% less efficient than DI units.
IDI engines became the engine of choice in small vehicle applications as a small engine could produce more power at higher speed providing a suitable power/weight ratio for such applications. Recent advances in fuel injection technology, which provide more precise fuel delivery, allow faster combustion within a DI engine. The improved efficiency of the DI cycle has spurred the fitment of such engines to become more common in small vehicles.