Ive been through nearly every variation of cooling upgrades to try and get a 6.5 TD in a Hummer to keep cool while working. Balanced Waterpump, Tanked Radiator, new pressure cap, Kennedy early engagement fan clutch, Duramax fan. Even a wired up fully 100 percent locked fan.
Its a basically stock engine. Dont get me wrong - it works and I drive it every day, but on a long hill or pulling a medium load the temp gauge climbs on a one way trip. And you have to pull over. Boring.
I did have a broken shroud that I tried to repair at one point and I had the idea to extend the shroud depth around the fan further. I fussed with it a bit and then replaced the shroud in the end (it was only 50 bucks new).
While doing this I found some good info on the internet from fan manufactures - I think Flexolite and Hayden, with general parameters on ideal fan shroud designs.
Guess where a Hummer fan shroud rates. It does not.
Its so far off on all counts Im amazed they move air on a good day. Fan blades should be 1" from the radiator. Huge Fail. Fan swept area should not be outside of Radiator surface area. Big fail. I estimate that nearly half the fan area is outside of the radiator area. Fan blades should be partly in and partly out of the shroud. I found this interesting. It seems a good portion of the air "spills" off the tips of the fan. The blade tips need to be partly in the open to allow this air to move.
The basic Hummer fan is 18-19 inches in diameter and all the air flows through a massive Prism shape from the leaned over Rad to the upright fan running off the front of the engine.
There are good designs out there of horizontal Rads that flow enough air to run in hot dusty conditions at redline all day long. I happen to have one. A CAT Skid-steer loader.
Enter the Hydraulic Fan Drive.
Now I see huge potential. With the fan no longer mechanically linked to the engine there are a multitude of benefits.
The fan can be moved to be flat against the Radiator.
The size constraints of an engine mounted fan change. I can move from a 19" Diameter fan (283sq inches) to a 24" diameter fan (452SQ INCHES!!!)
The fan is no longer restrained to operating at engine speed. It can be run slower or faster than the current rpm you are running at. This means faster than a viscous clutch fan a full lock up.
The fan motor can be reversed to blow leaves and pine needles out of the Rad stack.
Viscous (useless) fan clutch becomes a thing of the past.
I had been thinking of this since getting my H1 a couple years ago but a short clip of a H1 testing a hydraulic fan drive inspired me to move along a little. The test setup in the video was not fully implemented for reasons I'm exactly sure of. Something about components not being up to scratch.
Recently I saw a Cummins powered bus at a local Wrecker and salvaged some of the parts for my project.
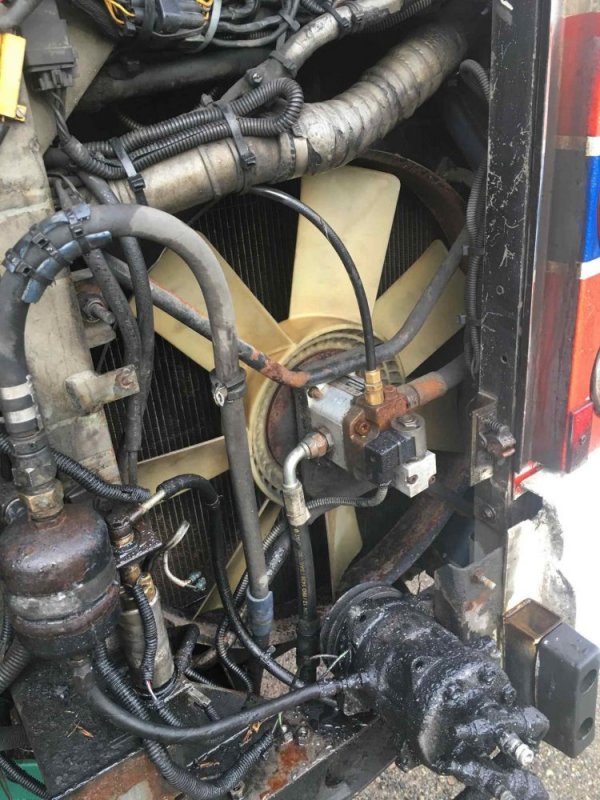
Its a basically stock engine. Dont get me wrong - it works and I drive it every day, but on a long hill or pulling a medium load the temp gauge climbs on a one way trip. And you have to pull over. Boring.
I did have a broken shroud that I tried to repair at one point and I had the idea to extend the shroud depth around the fan further. I fussed with it a bit and then replaced the shroud in the end (it was only 50 bucks new).
While doing this I found some good info on the internet from fan manufactures - I think Flexolite and Hayden, with general parameters on ideal fan shroud designs.
Guess where a Hummer fan shroud rates. It does not.
Its so far off on all counts Im amazed they move air on a good day. Fan blades should be 1" from the radiator. Huge Fail. Fan swept area should not be outside of Radiator surface area. Big fail. I estimate that nearly half the fan area is outside of the radiator area. Fan blades should be partly in and partly out of the shroud. I found this interesting. It seems a good portion of the air "spills" off the tips of the fan. The blade tips need to be partly in the open to allow this air to move.
The basic Hummer fan is 18-19 inches in diameter and all the air flows through a massive Prism shape from the leaned over Rad to the upright fan running off the front of the engine.
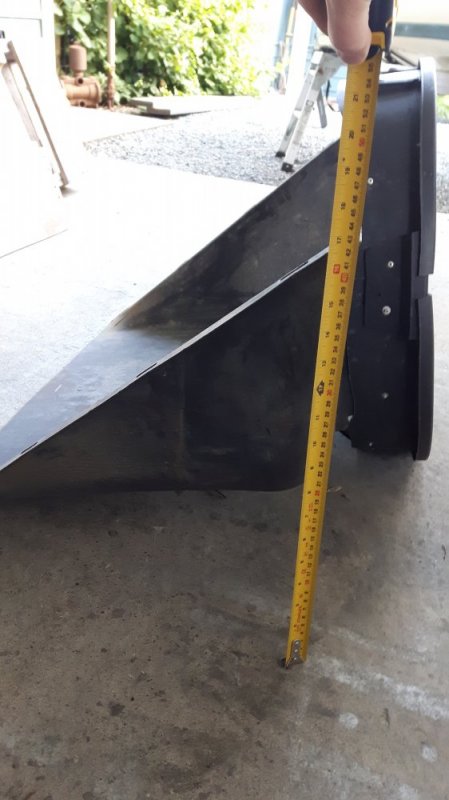
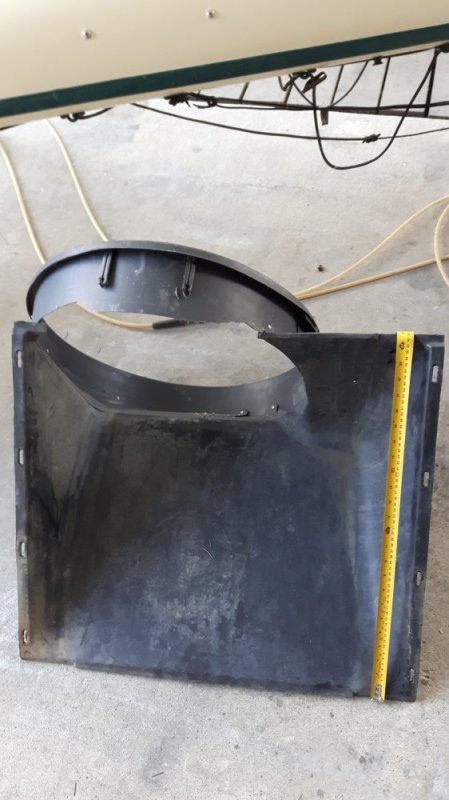
There are good designs out there of horizontal Rads that flow enough air to run in hot dusty conditions at redline all day long. I happen to have one. A CAT Skid-steer loader.
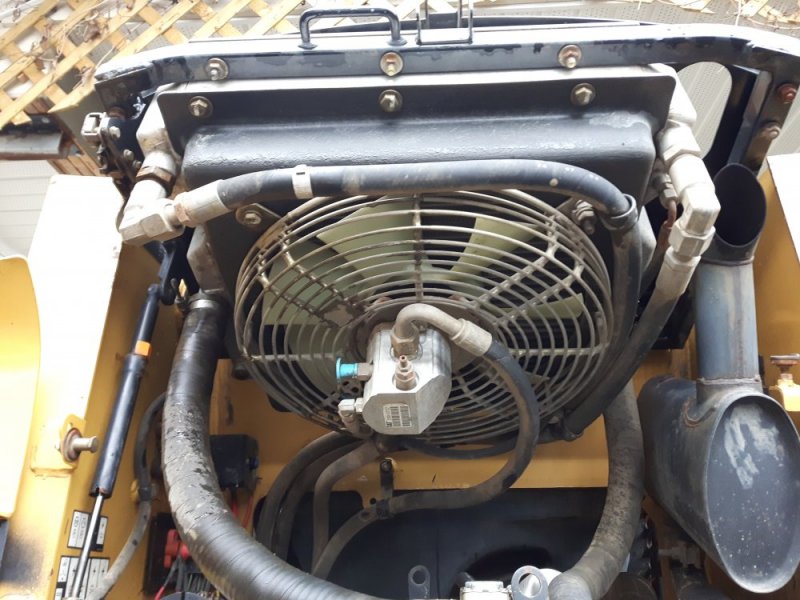
Enter the Hydraulic Fan Drive.
Now I see huge potential. With the fan no longer mechanically linked to the engine there are a multitude of benefits.
The fan can be moved to be flat against the Radiator.
The size constraints of an engine mounted fan change. I can move from a 19" Diameter fan (283sq inches) to a 24" diameter fan (452SQ INCHES!!!)
The fan is no longer restrained to operating at engine speed. It can be run slower or faster than the current rpm you are running at. This means faster than a viscous clutch fan a full lock up.
The fan motor can be reversed to blow leaves and pine needles out of the Rad stack.
Viscous (useless) fan clutch becomes a thing of the past.
I had been thinking of this since getting my H1 a couple years ago but a short clip of a H1 testing a hydraulic fan drive inspired me to move along a little. The test setup in the video was not fully implemented for reasons I'm exactly sure of. Something about components not being up to scratch.
Recently I saw a Cummins powered bus at a local Wrecker and salvaged some of the parts for my project.
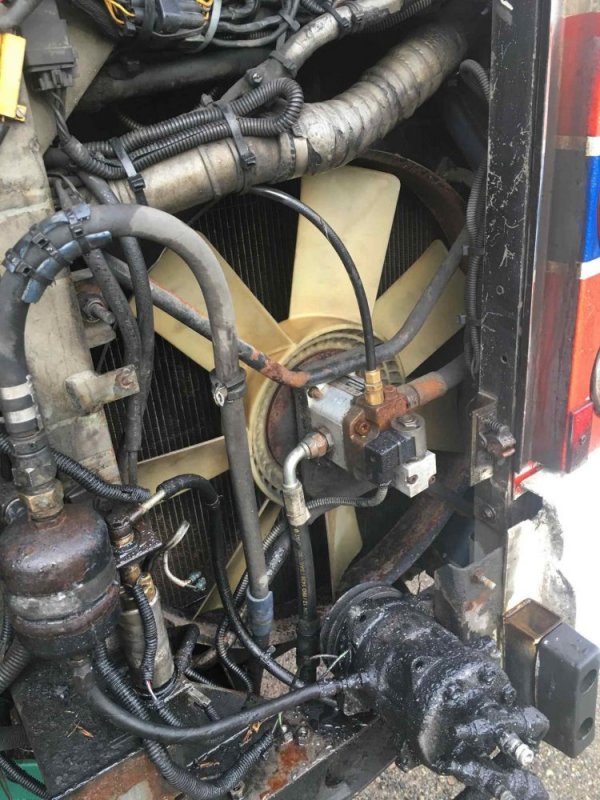