plstokes
Member
- Messages
- 64
- Reaction score
- 0
My wife surprised me with this new little welder that I had been looking at. I finally got it out of the box last night and laid a few beads. I am no welder and i have never welded with a wire welder but it seems like it's going to do pretty good. It's an inexpensive one from Harbor Freight but it should hold up fine for no more than I will be using it.
The welds don't look too good but maybe I'll get better, any tips or recommendations are welcomed.:agreed:
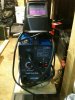
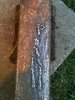
The welds don't look too good but maybe I'll get better, any tips or recommendations are welcomed.:agreed:
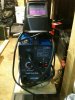
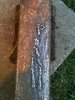