MrMarty51
Well-Known Member
I’m getting ready to get the 2000 K3500 into the garage to install the new cooling system uprated components.
In @Will L. s thread, a pic of the pump and the backing plate shows that the ports on one side are not matched.
Just looking for ideas and opinions if it would be a good idea to use the die grinder and remove minimal material until the ports match between the plate and the pump.
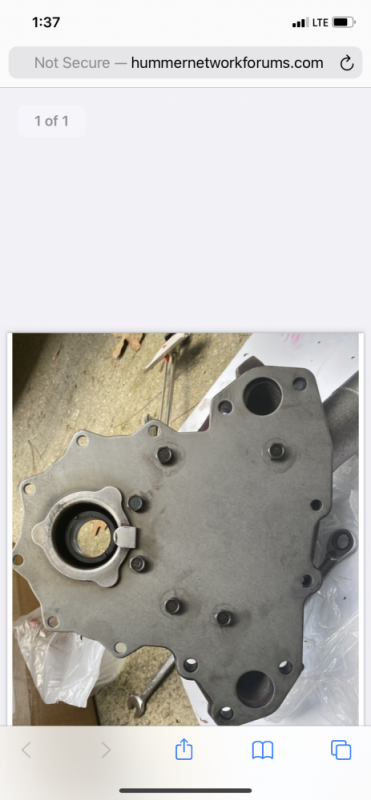
In @Will L. s thread, a pic of the pump and the backing plate shows that the ports on one side are not matched.
Just looking for ideas and opinions if it would be a good idea to use the die grinder and remove minimal material until the ports match between the plate and the pump.
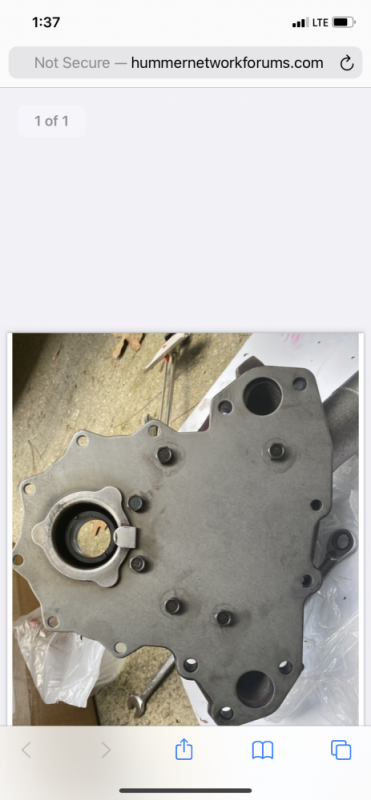