MrMarty51
Well-Known Member
And so, engine on stand and all freeze plugs removed.
Removed the oring from the freeze plug coolant heater and tried it in the various bores.
The original position was in the left bank, center hole and the element pointing downwards.
Removing the oring seal allowed me to move it freely from bore to bore and position it in any angle to the block.
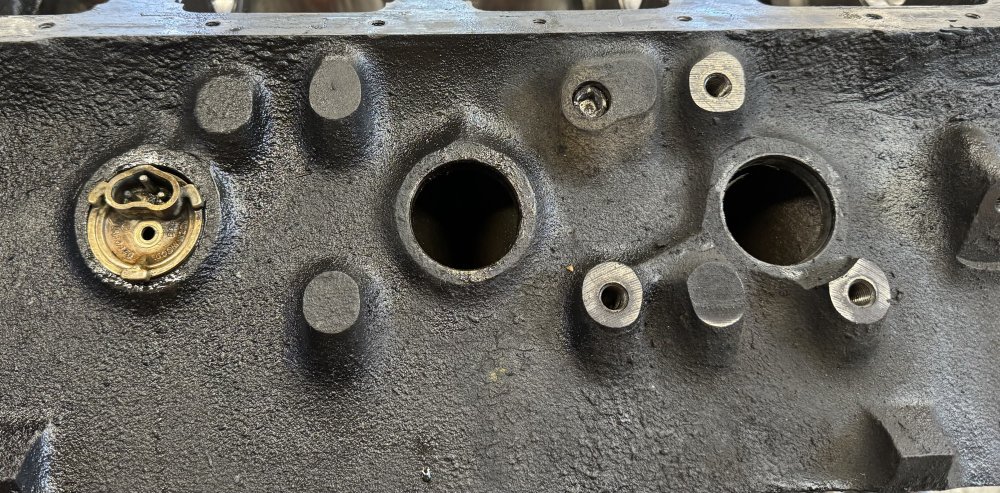
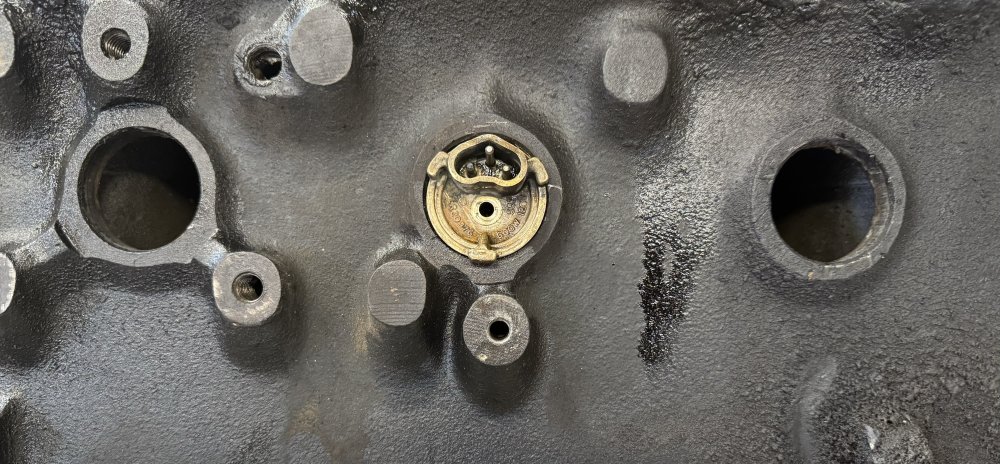
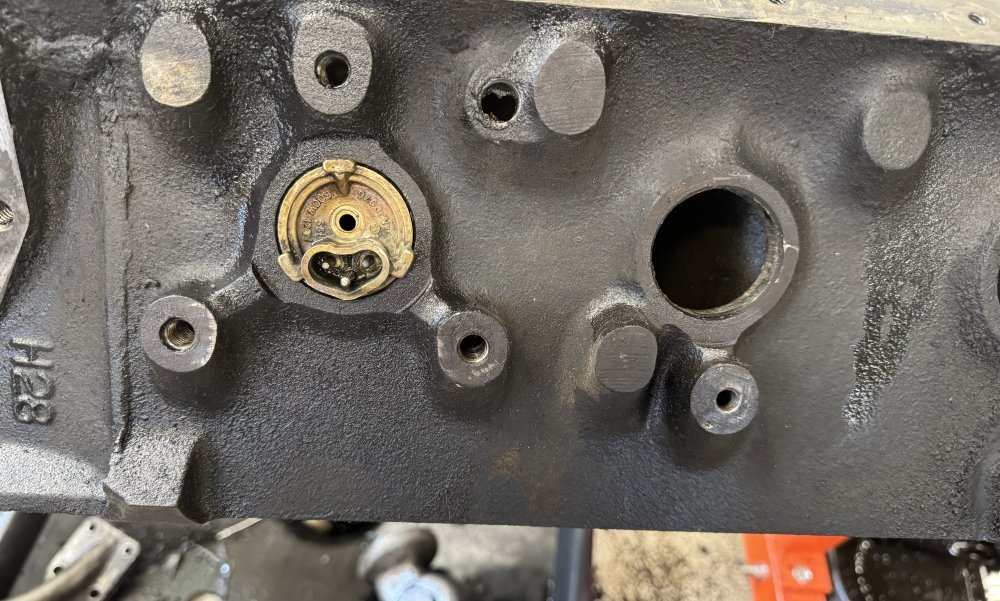

Aaand, My conclusion.
The bores for the freeze plugs are exactly centered between the cylinders.
The freeze plug heaters can be installed in any one or two, three four or six of the bores without interference as long as the element is pointed in the upward or downwards position. 90 degrees to the block flat surfaces, oil pan or head surfaces.
I might install four into this engine, burn on two at a time. If one of them burns out then link to another to continually run two.
Lets see, I’m near 73, four of those should run for longer than what My existence here on earth should be.


And so, that should end the time old debate of which holes to mount the engine coolant heater into.



Removed the oring from the freeze plug coolant heater and tried it in the various bores.
The original position was in the left bank, center hole and the element pointing downwards.
Removing the oring seal allowed me to move it freely from bore to bore and position it in any angle to the block.
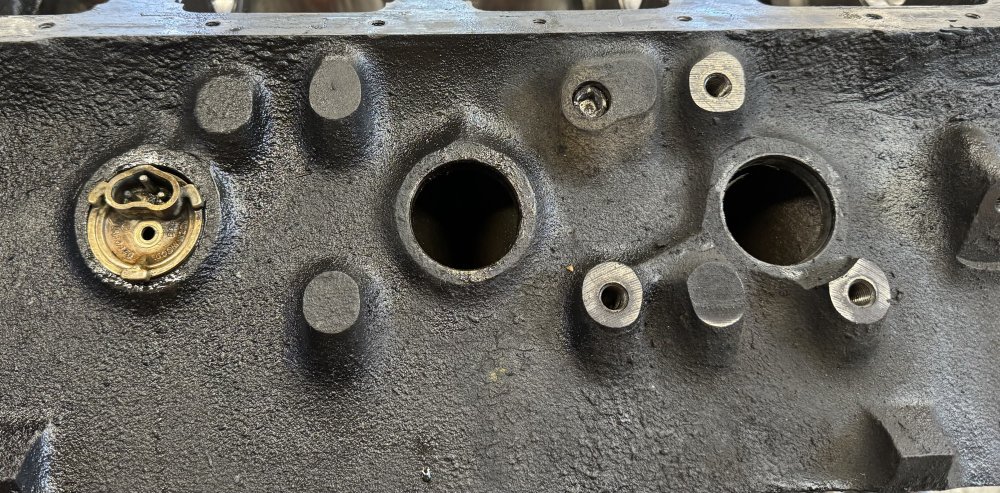
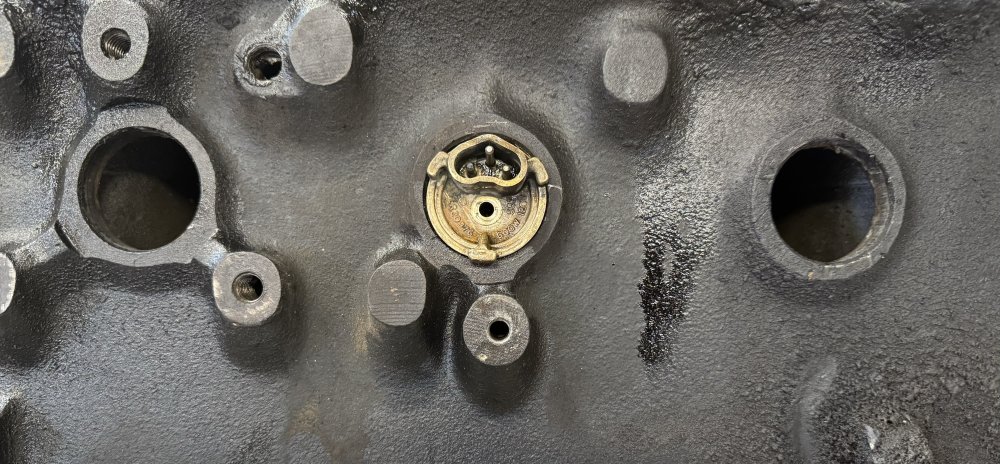
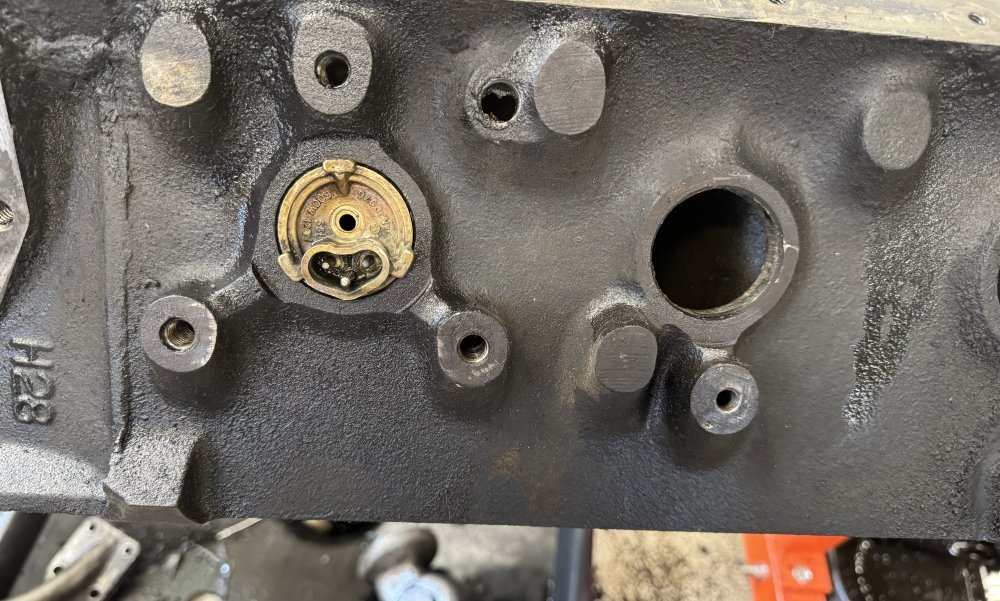

Aaand, My conclusion.
The bores for the freeze plugs are exactly centered between the cylinders.
The freeze plug heaters can be installed in any one or two, three four or six of the bores without interference as long as the element is pointed in the upward or downwards position. 90 degrees to the block flat surfaces, oil pan or head surfaces.
I might install four into this engine, burn on two at a time. If one of them burns out then link to another to continually run two.
Lets see, I’m near 73, four of those should run for longer than what My existence here on earth should be.



And so, that should end the time old debate of which holes to mount the engine coolant heater into.


