treegump
Romans 3:22-24
So, I'm building a headache rack to protect my back window. Using square tubing, 1/8" sidewalls, and will post exact measurements and more pictures after I finish on Saturday. I think I have 1x3 and 1x1 tubing...or something like that. The rectangler is for the 2 sides and top, and the square tubing is the lower rail and inside frame. I'm going to weld expanded metal to one side. Was thinking of welding it so that it sat between the rack frame and window, but thinking it'll be so that the welds can be seen from the bed...
We'll see.
2 questions that I've ran into.
1) When welding - I blew out a corner - just melted the heck out of it. Could I not fill it because I wouldn't allow it to cool down between beads? I probably sunk 10 welding rods into it, and didn't fix it till the 2nd scab. Spent 3 hrs trying to fix the sucker. Any tricks to fixing/filling holes when welding? Turn the current up/down? Add material somehow? Finally got it decent, but will fix it up more and finish it when I get back to it.
2) When mounting the headache rack, it appears everyone just uses the front bed rail holes, or even fasten into the bed sides themselves, but just the first foot or less. Doesn't look like there's any other anchor points. BUT - if something hits that headache rack hard at all (which it IS there for a reason), what prevents it from tearing up the bed rails and leaning against the window? My plan is/was to build a bracket __| kind of like that. And then use a bolt and use the existing hole to put an eye bolt in to anchor it in the hole. And for giggles, I'm going to use 3 | bolts (grade 5) in the front and attach that to a 1"x1" tube that I used to straighten/strengthen the front of the box.
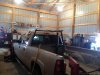
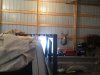
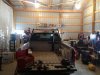
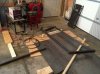

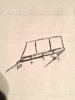
Thoughts or advice? Recommendations? When I have the opportunity, I will be purchasing some angle iron to put along my bed rails to strengthen them, but want to come up with a plan so I can put bed side extensions on securely, specifically for hauling brush, trash, and mainly firewood. It's hard to find ideas online...but maybe I'm just not typing in the right key words to find them. Still considering on building/buying a flatbed, but we'll see how much I use the truck when I get home.
2 questions that I've ran into.
1) When welding - I blew out a corner - just melted the heck out of it. Could I not fill it because I wouldn't allow it to cool down between beads? I probably sunk 10 welding rods into it, and didn't fix it till the 2nd scab. Spent 3 hrs trying to fix the sucker. Any tricks to fixing/filling holes when welding? Turn the current up/down? Add material somehow? Finally got it decent, but will fix it up more and finish it when I get back to it.
2) When mounting the headache rack, it appears everyone just uses the front bed rail holes, or even fasten into the bed sides themselves, but just the first foot or less. Doesn't look like there's any other anchor points. BUT - if something hits that headache rack hard at all (which it IS there for a reason), what prevents it from tearing up the bed rails and leaning against the window? My plan is/was to build a bracket __| kind of like that. And then use a bolt and use the existing hole to put an eye bolt in to anchor it in the hole. And for giggles, I'm going to use 3 | bolts (grade 5) in the front and attach that to a 1"x1" tube that I used to straighten/strengthen the front of the box.
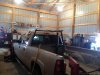
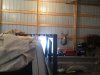
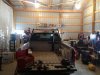
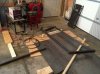

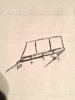
Thoughts or advice? Recommendations? When I have the opportunity, I will be purchasing some angle iron to put along my bed rails to strengthen them, but want to come up with a plan so I can put bed side extensions on securely, specifically for hauling brush, trash, and mainly firewood. It's hard to find ideas online...but maybe I'm just not typing in the right key words to find them. Still considering on building/buying a flatbed, but we'll see how much I use the truck when I get home.