DieselAmateur
She ain't revved 'til the rods are thrown...
After sitting on my shelf for 2 years, I finally got around to making this upgrade happen. Sadly the Sidewinder manifold is discontinued and no longer available from Banks, but hopefully this helps the few who already have one or are lucky enough to score a used one.
There are several others who did this upgrade years ago so credit goes to those who paved the way. I hope this can help folks in the future too.
Parts needed:
Banks Sidewinder Manifold, #51002-00
Van/ Hummer exhaust manifold, RH #10238373
GM EVO delete tube, GM #19168825
Power steering pressure hose from 97+, I used GATES 365460
2" vband connectors and clamp
2" 3 bolt exhaust flange
1 3/4" short sweep elbow
1 3/4" 45* pipe mandrel bent
One 1 3/4" to 2" exhaust coupler
Two 2" 60* mandrel bent exhaust pipes, 1' length each
Extra 2" pipe
2" stainless exhaust bellows
I live in the salt belt, so I elected to make the entire crossover pipe out of stainless. It will get exhaust wrap which I consider a necessity given how close it runs to the power steering line.
The first thing I addressed was the van/ hummer exhaust manifold. It has a tapered sealing surface to accept a flat face flare, like a turbo to a downpipe. So mating up to a vband flange out of the box is a no go
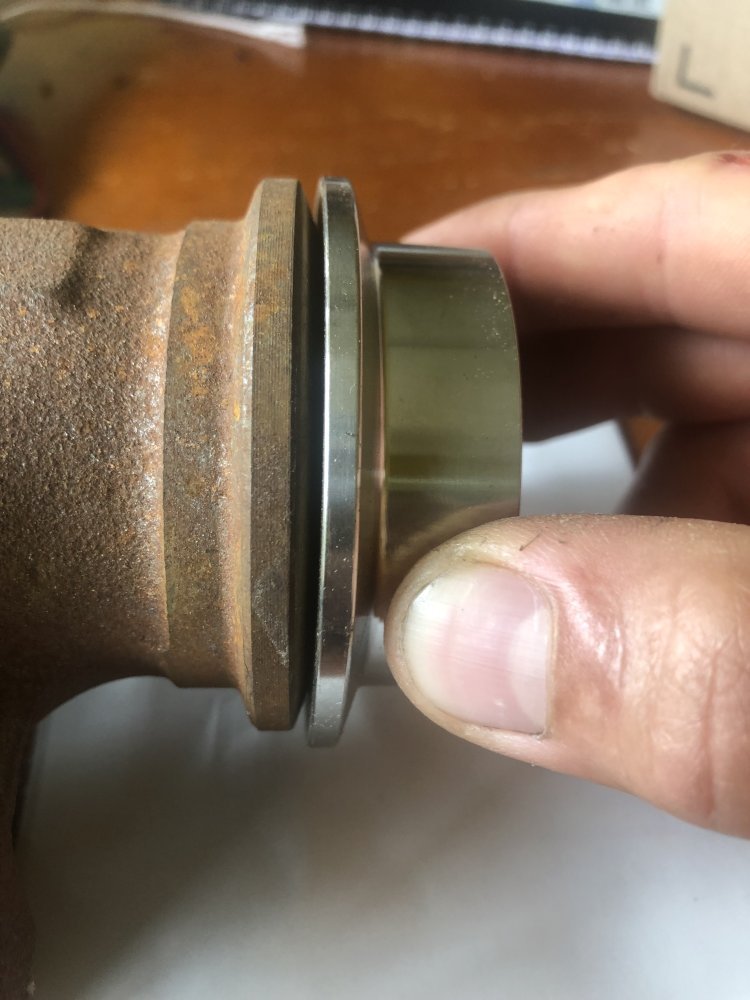
So what I did was take the manifold to a machine shop and have the flange milled down flat. I went this route because I wanted to be able to use a vband connection, and I wasn't sure stainless could take a flat face flare without cracking. Furthermore it proved difficult to find a shop around here that could do a flat flare, and given how I was going directly from the manifold to a short sweep elbow, flaring a curved piece of exhaust seemed more challenging than getting a face milled down.
There are several others who did this upgrade years ago so credit goes to those who paved the way. I hope this can help folks in the future too.
Parts needed:
Banks Sidewinder Manifold, #51002-00
Van/ Hummer exhaust manifold, RH #10238373
GM EVO delete tube, GM #19168825
Power steering pressure hose from 97+, I used GATES 365460
2" vband connectors and clamp
2" 3 bolt exhaust flange
1 3/4" short sweep elbow
1 3/4" 45* pipe mandrel bent
One 1 3/4" to 2" exhaust coupler
Two 2" 60* mandrel bent exhaust pipes, 1' length each
Extra 2" pipe
2" stainless exhaust bellows
I live in the salt belt, so I elected to make the entire crossover pipe out of stainless. It will get exhaust wrap which I consider a necessity given how close it runs to the power steering line.
The first thing I addressed was the van/ hummer exhaust manifold. It has a tapered sealing surface to accept a flat face flare, like a turbo to a downpipe. So mating up to a vband flange out of the box is a no go
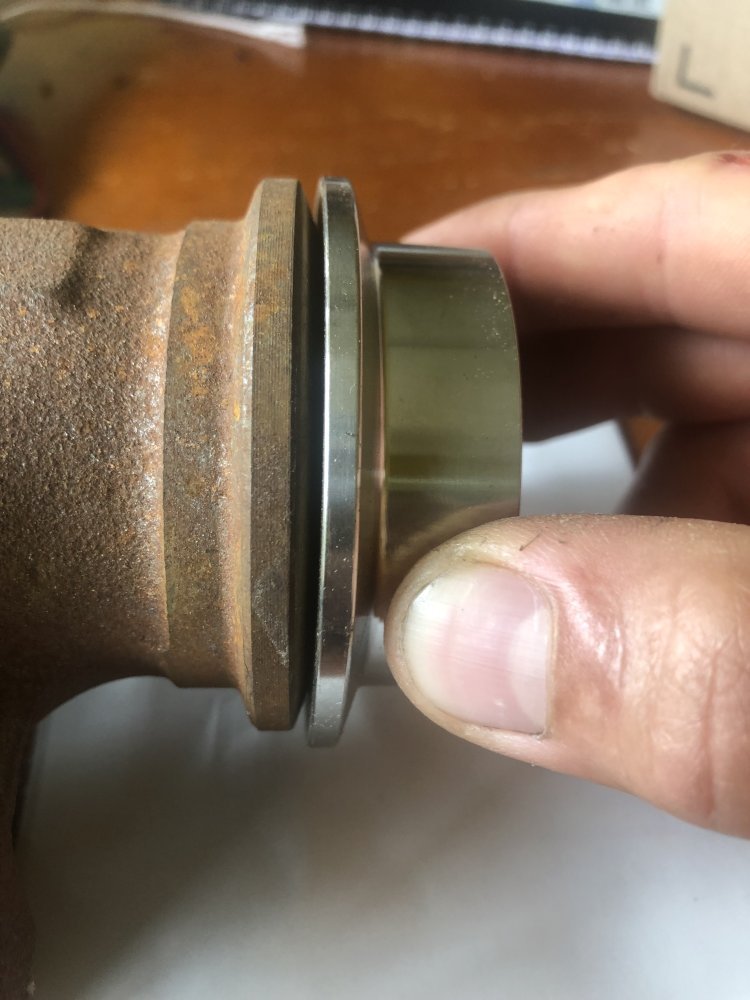
So what I did was take the manifold to a machine shop and have the flange milled down flat. I went this route because I wanted to be able to use a vband connection, and I wasn't sure stainless could take a flat face flare without cracking. Furthermore it proved difficult to find a shop around here that could do a flat flare, and given how I was going directly from the manifold to a short sweep elbow, flaring a curved piece of exhaust seemed more challenging than getting a face milled down.